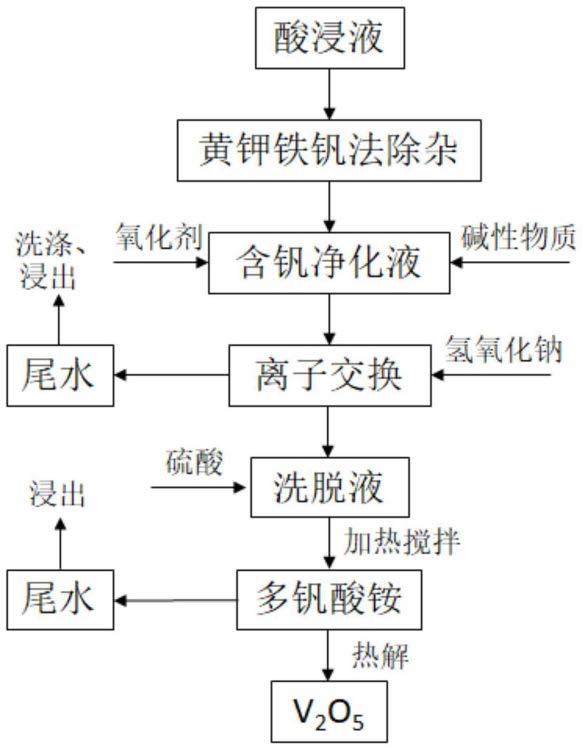
1.本發(fā)明屬于五氧化二釩制備領(lǐng)域,涉及一種從石煤酸浸液中提取五氧化二釩的方法。
背景技術(shù):
2.五氧化二釩廣泛用于冶金、化工等行業(yè),用作合金添加劑、有機化工的催化劑、無機化學(xué)品、搪瓷和磁性材料等。石煤是一種多金屬共生礦,是提取五氧化二釩的主要原料之一。石煤提釩工藝主要有焙燒法和酸浸法兩大類。焙燒法由于存在焙燒過程生成cl2、hcl、so2等氣體造成環(huán)境污染以及釩回收率低的缺點,逐漸被酸浸法所取代。
3.在石煤酸浸提釩工藝中,含釩浸出液有較高濃度的鐵、鈉、鉀等雜質(zhì),其中鐵雜質(zhì)對后續(xù)離子交換過程有很大的影響。比如鐵氧化物以懸浮形態(tài)進(jìn)入交換床,由于樹脂吸附的作用,會堵塞樹脂微孔。在解吸過程中,鐵離子不能被完全交換出來,且吸附時間越長越難出去,容易造成樹脂中毒?,F(xiàn)有傳統(tǒng)富集含釩液體的方法都會加入除雜劑,選用石灰或碳酸鈣中和多余的酸將ph值控制在合適的范圍,嚴(yán)格控制液體中鐵離子的含量,但這會造成釩的沉淀損失,出現(xiàn)大量的中和渣,增加流程環(huán)節(jié),增大藥劑消耗量,產(chǎn)生二次污染。富集后的液體進(jìn)行銨鹽沉釩,尾水循環(huán)困難。這些方法存在成本高、水循環(huán)率低、污染大、釩提取率低等缺陷。
技術(shù)實現(xiàn)要素:
4.為了克服現(xiàn)有技術(shù)的不足,本發(fā)明提供一種在較強酸性條件下直接對有一定溫度的含釩浸出液進(jìn)行除雜富集的方法。本發(fā)明采用黃鉀鐵礬法除雜,經(jīng)黃鉀鐵礬法除雜后的液體,采用中和劑調(diào)節(jié)ph值、氧化劑氧化后用于離子交換,得到高濃度釩液。無氨沉釩后尾水可循環(huán)用于浸出過程。本發(fā)明的方法釩的提取率高,避免中和過程出現(xiàn)的大量中和渣,縮短了流程,減少了物料消耗,可徹底消除氨氮廢水問題,保護環(huán)境,大幅降低了生產(chǎn)成本。
5.具體而言,本發(fā)明提供一種從石煤中提取釩的方法,所述方法包括以下步驟:
6.(1)浸出:使用包含硫酸和助浸劑的酸性溶液對石煤粉進(jìn)行浸出,經(jīng)固液分離得到酸浸液;
7.(2)黃鉀鐵礬法除雜:使步驟(1)得到的酸浸液在50~80℃保溫6~12h,期間ph控制為0.5~1.5,形成黃鐵礬沉淀,經(jīng)固液分離得到含釩凈化液;
8.(3)中和氧化:將步驟(2)得到的含釩凈化液的ph值調(diào)節(jié)至1.5~2.5,再加入氧化劑將溶液中的低價釩氧化為五價釩,得到含釩清液;
9.(4)離子交換吸附:使用離子交換樹脂吸附步驟(3)得到的含釩清液中的釩化合物;
10.(5)離子交換解吸:使用解吸劑對步驟(4)中吸附后的離子交換樹脂進(jìn)行洗脫,得到富集了釩的洗脫液。
11.在一個或多個實施方案中,步驟(1)中,石煤粉的粒度為40~100目。
12.在一個或多個實施方案中,步驟(1)中,硫酸用量為石煤粉質(zhì)量的20~50%。
13.在一個或多個實施方案中,步驟(1)中,助浸劑的用量為石煤粉質(zhì)量的1~5%。
14.在一個或多個實施方案中,步驟(1)中,所述助浸劑為氯酸鈉和/或氯酸鉀。
15.在一個或多個實施方案中,步驟(1)中,浸出體系的料液比為1:1~1:2。
16.在一個或多個實施方案中,步驟(1)中,浸出溫度為80~100℃。
17.在一個或多個實施方案中,步驟(1)中,浸出時間為6~24小時。
18.在一個或多個實施方案中,步驟(1)還包括:將酸浸液的ph值調(diào)節(jié)至0.5~1.5,和/或?qū)⑺峤旱臏囟瓤刂茷?0~80℃。
19.在一個或多個實施方案中,步驟(2)中,所述黃鐵礬包括黃鉀鐵礬和黃鈉鐵礬。
20.在一個或多個實施方案中,步驟(2)中,在保溫釜中進(jìn)行黃鐵礬的沉淀反應(yīng),所述保溫釜優(yōu)選具有加熱功能。
21.在一個或多個實施方案中,步驟(3)中,添加堿性物質(zhì)調(diào)節(jié)含釩凈化液的ph至1.5~2.5。
22.在一個或多個實施方案中,步驟(3)中,所述堿性物質(zhì)選自na2co3、nahco3和naoh中的一種或多種。
23.在一個或多個實施方案中,步驟(3)中,加入的氧化劑為選自h2o2、naclo和naclo3中的一種或多種。
24.在一個或多個實施方案中,步驟(3)中,氧化劑的添加量為將溶液中的低價釩氧化為五價釩所需的理論用量的1.2~2倍。
25.在一個或多個實施方案中,步驟(4)中,使用大孔強堿性苯乙烯系陰離子交換樹脂進(jìn)行離子交換吸附。
26.在一個或多個實施方案中,步驟(4)中,將吸附后的尾水用于步驟(1)中的浸出過程和/或用于洗滌步驟(1)中固液分離后的礦渣。
27.在一個或多個實施方案中,步驟(5)中,使用質(zhì)量分?jǐn)?shù)為5~20%的naoh溶液作為解吸劑。
28.在一個或多個實施方案中,所述方法還包括以下步驟:
29.(6)沉釩:將步驟(5)得到的洗脫液中的釩以多釩酸銨的形式沉淀出來。
30.在一個或多個實施方案中,所述沉釩為無氨沉釩,所述無氨沉釩包括:將洗脫液的ph調(diào)節(jié)至1.5~2.1后,加熱至80~100℃攪拌,使溶液中的釩以多釩酸銨的形式沉淀出來;優(yōu)選地,將沉釩尾水用于步驟(1)中的浸出過程。
31.在一個或多個實施方案中,所述方法還包括以下步驟:
32.(7)多釩酸銨熱解:對多釩酸銨加熱使之分解得到五氧化二釩。
附圖說明
33.圖1為本發(fā)明一些實施方案中的石煤酸浸液提釩工藝的流程示意圖。
具體實施方式
34.為使本領(lǐng)域技術(shù)人員可了解本發(fā)明的特點及效果,以下謹(jǐn)就說明書及權(quán)利要求書中提及的術(shù)語及用語進(jìn)行一般性的說明及定義。除非另有指明,否則文中使用的所有技術(shù)
及科學(xué)上的字詞,均為本領(lǐng)域技術(shù)人員對于本發(fā)明所了解的通常意義,當(dāng)有沖突情形時,應(yīng)以本說明書的定義為準(zhǔn)。
35.本文描述和公開的理論或機制,無論是對或錯,均不應(yīng)以任何方式限制本發(fā)明的范圍,即本發(fā)明內(nèi)容可以在不為任何特定的理論或機制所限制的情況下實施。
36.本文中,“包含”、“包括”、“含有”以及類似的用語涵蓋了“基本由
……
組成”和“由
……
組成”的意思,例如,當(dāng)本文公開了“a包含b和c”時,“a基本由b和c組成”和“a由b和c組成”應(yīng)當(dāng)認(rèn)為已被本文所公開。
37.本文中,所有以數(shù)值范圍或百分比范圍形式界定的特征如數(shù)值、數(shù)量、含量與濃度僅是為了簡潔及方便。據(jù)此,數(shù)值范圍或百分比范圍的描述應(yīng)視為已涵蓋且具體公開所有可能的次級范圍及范圍內(nèi)的個別數(shù)值(包括整數(shù)與分?jǐn)?shù))。
38.本文中,若無特別說明,百分比是指質(zhì)量百分比,比例是指質(zhì)量比。
39.本文中,當(dāng)描述實施方案或?qū)嵤├龝r,應(yīng)理解,其并非用來將本發(fā)明限定于這些實施方案或?qū)嵤├?。相反地,本發(fā)明所描述的方法及材料的所有的替代物、改良物及均等物,均可涵蓋于權(quán)利要求書所限定的范圍內(nèi)。
40.本文中,為使描述簡潔,未對各個實施方案或?qū)嵤├械母鱾€技術(shù)特征的所有可能的組合都進(jìn)行描述。因此,只要這些技術(shù)特征的組合不存在矛盾,各個實施方案或?qū)嵤├械母鱾€技術(shù)特征可以進(jìn)行任意的組合,所有可能的組合都應(yīng)當(dāng)認(rèn)為是本說明書記載的范圍。
41.本發(fā)明的從石煤中提取釩的方法包括以下浸出步驟、除雜步驟、中和氧化步驟、離子交換吸附步驟和離子交換解吸步驟。
42.浸出步驟中,本發(fā)明使用包含硫酸和助浸劑的酸性溶液對石煤粉進(jìn)行浸出,經(jīng)固液分離得到酸浸液。用于浸出的石煤粉的粒度優(yōu)選為40~100目,例如60目、80目??梢圆捎枚跗拼制吩贊穹ㄇ蚰サ确绞綄⑹褐瞥删哂心繕?biāo)粒度的石煤粉。本發(fā)明中,用于浸出的酸性溶液為包含硫酸和助浸劑的水溶液。硫酸用量優(yōu)選為石煤粉質(zhì)量的20~50%,例如22%、25%、30%、40%。助浸劑的用量優(yōu)選為石煤粉質(zhì)量的1~5%,例如2%、3%、4%。浸出體系的料液比優(yōu)選為1:1~1:2,例如1:1.5??刂屏蛩嵊昧俊⒅┯昧亢土弦罕扔欣谔嵘褐锈C的浸出率,同時為后續(xù)黃鉀鐵礬法除雜提供合適的條件。助浸劑的作用是增加浸出效果。可以使用本領(lǐng)域已知的助浸劑。助浸劑優(yōu)選選自氯酸鈉和氯酸鉀。浸出所用的水可以來自于后續(xù)離子交換吸附步驟中產(chǎn)生的離子交換尾水或后續(xù)對浸出后固液分離得到的礦渣進(jìn)行洗滌得到的洗水。在一些實施方案中,浸出體系為石煤粉、硫酸、助浸劑和水源的混合物。浸出溫度優(yōu)選為80~100℃、例如85℃、90℃、95℃,這有利于提升釩的浸出率,并提供黃鉀鐵礬法除雜過程所需的熱量。浸出時間可以為6~24h,例如12h、16h、20h。浸出可以在攪拌條件下進(jìn)行。
43.浸出完成后對浸出后的料液進(jìn)行固液分離,得到酸浸液和礦渣。例如可以采用先使用帶式真空
過濾機過濾,濾液再經(jīng)廂式壓濾機精壓的方式進(jìn)行固液分離??梢詫ΦV渣進(jìn)行水洗,例如可以采用后續(xù)離子交換吸附步驟中產(chǎn)生的離子交換尾水對礦渣進(jìn)行洗滌,洗滌的方式可以是一級或多級(例如二級、三級、四級、五級)逆流洗滌。洗滌所得的洗水可用于浸出過程。
44.在一些實施方案中,固液分離后酸浸液的ph在0.5~1.5之間,則可待溫度降低至
50~80℃后使酸浸液進(jìn)入黃鉀鐵礬法除雜步驟。在一些實施方案中,固液分離后酸浸液的ph不在0.5~1.5之間,則將酸浸液的ph調(diào)至0.5~1.5之間并使溫度降低至50~80℃,然后使酸浸液進(jìn)入黃鉀鐵礬法除雜步驟。
45.本發(fā)明中,黃鉀鐵礬法除雜是使酸浸液在一定的溫度和ph條件下保溫靜置一段時間,使酸浸液中的鐵等雜質(zhì)形成黃鐵礬沉淀,再分離去除沉淀得到含釩凈化液的步驟。保溫靜置期間,酸浸液的溫度控制為50~80℃、例如60℃、70℃,ph控制為0.5~1.5、例如0.6、0.7、0.8、0.9、1.0、1.1、1.2、1.3、1.4,該溫度和ph條件下酸浸液的鐵等雜質(zhì)能夠形成黃鐵礬沉淀。本發(fā)明中,黃鐵礬包括黃鉀鐵礬(kfe3(so4)2(oh)6)和黃鈉鐵礬(nafe3(so4)2(oh)6)。保溫時間可以為6~12h,例如8h、10h。黃鐵礬沉淀反應(yīng)可以在在保溫釜中進(jìn)行。保溫釜隔熱效果好,基本無需對酸浸液進(jìn)行加熱。為了工藝運行穩(wěn)定,保溫釜優(yōu)選具有加熱功能。
46.本發(fā)明在進(jìn)行離子交換吸附前,先對黃鉀鐵礬法除雜得到的含釩凈化液進(jìn)行中和氧化,將含釩凈化液的ph值調(diào)節(jié)至1.5~2.5、例如1.8、2.0、2.2,再加入氧化劑將溶液中的低價釩氧化為五價釩,得到含釩清液。中和氧化的目的是調(diào)節(jié)ph值,進(jìn)一步凈化。用于調(diào)節(jié)ph的中和劑為堿性物質(zhì),選自na2co3、nahco3和naoh中的一種或多種。氧化劑優(yōu)選選自h2o2、naclo和naclo3中的一種或多種。氧化劑的添加量優(yōu)選為將溶液中的低于五價的低價釩(主要是四價釩)氧化為五價釩所需的理論用量的1.2~2倍、例如1.5倍。
47.離子交換吸附步驟中,使用離子交換樹脂吸附中和氧化后的含釩清液中的釩化合物。優(yōu)選使用大孔強堿性苯乙烯系陰離子交換樹脂進(jìn)行離子交換吸附。吸附后的含酸尾水可回用于洗滌浸出后的礦渣,或回用于浸出過程。待離子交換吸附尾水中釩濃度降低至工藝要求、例如0.1g v2o5/l以下時,可停止樹脂吸附過程,開始樹脂解吸再生過程。
48.離子交換解吸步驟中,使用解吸劑對吸附后的離子交換樹脂進(jìn)行洗脫,得到富集了釩的洗脫液(一種高濃度的含釩液體),同時離子交換樹脂獲得再生。優(yōu)選地,使用質(zhì)量分?jǐn)?shù)為5~20%、例如10%、15%的naoh溶液作為解吸劑。待洗脫液中釩濃度達(dá)到工藝要求、例如≥50g v2o5/l時,可停止解吸過程。
49.通過上述步驟獲得了含高濃度釩的洗脫液后,本發(fā)明的從石煤中提取釩的方法還可以進(jìn)一步包括沉釩步驟:將洗脫液中的釩以多釩酸銨的形式沉淀出來。優(yōu)選地,沉釩為無氨沉釩,即將洗脫液的ph調(diào)節(jié)至1.5~2.1、例如1.8后,加熱至80~100℃、例如90℃攪拌,利用釩的溶解度低的原理,溶液中釩以多釩酸銨的形式沉淀出來。將沉釩尾水為酸性液體,經(jīng)澄清后,可回用于浸出過程。
50.本發(fā)明的從石煤中提取釩的方法還可以包括多釩酸銨熱解步驟:對多釩酸銨加熱使之受熱分解得到五氧化二釩。加熱可以是在450~550℃下高溫灼燒2~5h、例如3h以上。
51.本發(fā)明通過對含有較高濃度的鐵、鈉、鉀等雜質(zhì)的石煤酸浸液進(jìn)行黃鉀鐵礬法除雜,大大簡化了酸浸液預(yù)處理過程,縮短了流程,不加入除雜劑,避免了二次污染。無氨沉釩后尾水循環(huán)可用于浸出過程,徹底消除了氨氮廢水問題,保護環(huán)境,大幅降低了生產(chǎn)成本。
52.本發(fā)明與已有的技術(shù)相比具有以下優(yōu)點及有益效果:
53.1、對含有較高濃度的鐵、鈉、鉀等雜質(zhì)的酸浸液,通過黃鉀鐵礬法除雜,大大簡化了酸浸液預(yù)處理過程,避免中和過程出現(xiàn)的大量中和渣,縮短了流程,避免了二次污染,有效降低了鐵離子濃度,解決了鐵離子對樹脂影響的問題,離子交換尾水循環(huán)用于浸出,環(huán)境友好。
54.2、無氨沉釩后尾水循環(huán)用于浸出過程,徹底消除了氨氮廢水問題,系統(tǒng)實現(xiàn)了閉路循環(huán),釩的收率提高。
55.3、黃鉀鐵礬法除雜過程中,充分利用了浸出過程的熱量,常規(guī)運行無需外加蒸汽,節(jié)約了能源消耗。浸出液ph值控制在0.5~1.5,滿足除雜過程的酸性條件,簡化了操作流程,控制簡便。
56.4、保證了除鐵的效果,在中和劑的選用上,采用了na2co3、nahco3、naoh替代常規(guī)的石灰、碳酸鈣,避免現(xiàn)有工藝中和過程出現(xiàn)的大量中和渣,環(huán)境友好。
57.下文將以具體實施例的方式闡述本發(fā)明。應(yīng)理解,這些實施例僅僅是闡述性的,并非意圖限制本發(fā)明的范圍。實施例中所用到的方法、試劑和材料,除非另有說明,否則為本領(lǐng)域常規(guī)的方法、試劑和材料。實施例中的原料化合物均可通過市售途徑購得。
58.實施例1
59.本實施例按照圖1所示的流程從石煤中提取釩:
60.1、石煤浸出:含釩(v2o50.96%)的石煤經(jīng)顎式
破碎機粗破后,濕法球磨至粒度80目,加入質(zhì)量為石煤質(zhì)量25%的硫酸和2%的助浸劑氯酸鈉,加水將料液比控制在1:1.5左右,加熱至95℃左右,攪拌浸出,浸出時間為16h;
61.2、固液分離及酸浸液預(yù)處理:使用帶式真空過濾機對浸出后的料液進(jìn)行固液分離,濾液再經(jīng)廂式壓濾機精壓,得到酸浸液和礦渣;礦渣采用離子交換尾水四級逆流洗滌,洗水用于浸出過程;經(jīng)檢測酸浸液ph值為0.9,待酸浸液溫度由95℃降低至70℃左右,進(jìn)入保溫釜進(jìn)行除雜;
62.3、黃鉀鐵礬法除雜:在保溫釜內(nèi),酸浸液在70℃保溫靜置8h,期間ph值保持在0.8~0.9之間,雜質(zhì)以kfe3(so4)2(oh)6和nafe3(so4)2(oh)6為主要形式沉淀下來,經(jīng)離心機過濾得含釩凈化液;保溫釜隔熱效果好,基本不再額外加入蒸汽進(jìn)行保溫,為了工藝運行穩(wěn)定,保溫釜具備蒸汽加熱的裝置條件;
63.4、中和氧化:向含釩凈化液中加入na2co3調(diào)節(jié)ph值至2.0左右,再加入理論量1.5倍的h2o2使液體中的v
4+
氧化為v
5+
,得到含釩清液;
64.5、離子交換吸附:將含釩清液進(jìn)入裝填有大孔強堿性苯乙烯系陰離子交換樹脂的離子交換柱進(jìn)行離子交換吸附,吸附后的尾水用于洗滌、浸出過程;當(dāng)尾水中釩濃度達(dá)到0.1g v2o5/l時,樹脂吸附過程停止,開始樹脂解吸再生過程;
65.6、離子交換解吸再生:使用質(zhì)量分?jǐn)?shù)為10%的naoh解吸液作為解吸劑進(jìn)入離子交換柱對吸附后的樹脂進(jìn)行洗脫,得到的洗脫液為含釩濃度符合工藝要求(≥50g v2o5/l)的高濃度含釩液體,同時樹脂獲得再生。
66.7、無氨沉釩:向洗脫液中加入硫酸調(diào)節(jié)ph值至1.8左右,液體加熱至90℃左右,攪拌,液體中的釩以多釩酸銨形式沉淀,離心機過濾得到固體多釩酸銨;沉釩尾水回流循環(huán)用于浸出過程。
67.8、多釩酸銨熱解:將多釩酸銨置于電鍛爐內(nèi),在500℃左右的溫度下高溫灼燒3h以上,得到純度為98.7%的v2o5產(chǎn)品。
68.實施例2
69.1、石煤浸出:含釩(v2o50.96%)的石煤經(jīng)顎式破碎機粗破后,濕法球磨至粒度80目,加入質(zhì)量為石煤質(zhì)量30%的硫酸和2%的助浸劑氯酸鈉,加水將料液比控制在1:1左右,
加熱至95℃左右,攪拌浸出,浸出時間為16h;
70.2、固液分離及酸浸液預(yù)處理:使用帶式真空過濾機對浸出后的料液進(jìn)行固液分離,濾液再經(jīng)廂式壓濾機精壓,得到酸浸液和礦渣;礦渣采用離子交換尾水四級逆流洗滌,洗水用于浸出過程;經(jīng)檢測酸浸液ph值為0.6,待酸浸液溫度由95℃降低至50℃左右,進(jìn)入保溫釜進(jìn)行除雜;
71.3、黃鉀鐵礬法除雜:在保溫釜內(nèi),酸浸液在50℃保溫靜置12h,期間ph值保持在0.5~0.6之間,雜質(zhì)以kfe3(so4)2(oh)6和nafe3(so4)2(oh)6為主要形式沉淀下來,經(jīng)離心機過濾得含釩凈化液;保溫釜隔熱效果好,基本不再額外加入蒸汽進(jìn)行保溫,為了工藝運行穩(wěn)定,保溫釜具備蒸汽加熱的裝置條件;
72.4、中和氧化:向含釩凈化液中加入na2co3調(diào)節(jié)ph值至2.0左右,再加入理論量1.5倍的h2o2使液體中的v
4+
氧化為v
5+
,得到含釩清液;
73.5、離子交換吸附:將含釩清液進(jìn)入裝填有大孔強堿性苯乙烯系陰離子交換樹脂的離子交換柱進(jìn)行離子交換吸附,吸附后的尾水用于洗滌、浸出過程;當(dāng)尾水中釩濃度達(dá)到0.1g v2o5/l時,樹脂吸附過程停止,開始樹脂解吸再生過程;
74.6、離子交換解吸再生:使用質(zhì)量分?jǐn)?shù)為10%的naoh解吸液作為解吸劑進(jìn)入離子交換柱對吸附后的樹脂進(jìn)行洗脫,得到的洗脫液為含釩濃度符合工藝要求(≥50g v2o5/l)的高濃度含釩液體,同時樹脂獲得再生。
75.7、無氨沉釩:向洗脫液中加入硫酸調(diào)節(jié)ph值至1.8左右,液體加熱至90℃左右,攪拌,液體中的釩以多釩酸銨形式沉淀,離心機過濾得到固體多釩酸銨;沉釩尾水回流循環(huán)用于浸出過程。
76.8、多釩酸銨熱解:將多釩酸銨置于電鍛爐內(nèi),在500℃左右的溫度下高溫灼燒3h以上,得到純度為98.5%的v2o5產(chǎn)品。
77.實施例3
78.1、石煤浸出:含釩(v2o50.96%)的石煤經(jīng)顎式破碎機粗破后,濕法球磨至粒度80目,加入質(zhì)量為石煤質(zhì)量22%的硫酸和2%的助浸劑氯酸鈉,加水將料液比控制在1:1.2左右,加熱至95℃左右,攪拌浸出,浸出時間為16h;
79.2、固液分離及酸浸液預(yù)處理:使用帶式真空過濾機對浸出后的料液進(jìn)行固液分離,濾液再經(jīng)廂式壓濾機精壓,得到酸浸液和礦渣;礦渣采用離子交換尾水四級逆流洗滌,洗水用于浸出過程;經(jīng)檢測酸浸液ph值為1.5,待酸浸液溫度由95℃降低至80℃左右,進(jìn)入保溫釜進(jìn)行除雜;
80.3、黃鉀鐵礬法除雜:在保溫釜內(nèi),酸浸液在80℃保溫靜置6h,期間ph值保持在1.4~1.5之間,雜質(zhì)以kfe3(so4)2(oh)6和nafe3(so4)2(oh)6為主要形式沉淀下來,經(jīng)離心機過濾得含釩凈化液;保溫釜隔熱效果好,基本不再額外加入蒸汽進(jìn)行保溫,為了工藝運行穩(wěn)定,保溫釜具備蒸汽加熱的裝置條件;
81.4、中和氧化:向含釩凈化液中加入na2co3調(diào)節(jié)ph值至2.0左右,再加入理論量1.5倍的h2o2使液體中的v
4+
氧化為v
5+
,得到含釩清液;
82.5、離子交換吸附:將含釩清液進(jìn)入裝填有大孔強堿性苯乙烯系陰離子交換樹脂的離子交換柱進(jìn)行離子交換吸附,吸附后的尾水用于洗滌、浸出過程;當(dāng)尾水中釩濃度達(dá)到0.1g v2o5/l時,樹脂吸附過程停止,開始樹脂解吸再生過程;
83.6、離子交換解吸再生:使用質(zhì)量分?jǐn)?shù)為10%的naoh解吸液作為解吸劑進(jìn)入離子交換柱對吸附后的樹脂進(jìn)行洗脫,得到的洗脫液為含釩濃度符合工藝要求(≥50g v2o5/l)的高濃度含釩液體,同時樹脂獲得再生。
84.7、無氨沉釩:向洗脫液中加入硫酸調(diào)節(jié)ph值至1.8左右,液體加熱至90℃左右,攪拌,液體中的釩以多釩酸銨形式沉淀,離心機過濾得到固體多釩酸銨;沉釩尾水回流循環(huán)用于浸出過程。
85.8、多釩酸銨熱解:將多釩酸銨置于電鍛爐內(nèi),在500℃左右的溫度下高溫灼燒3h以上,得到純度為98.8%的v2o5產(chǎn)品。技術(shù)特征:
1.一種從石煤中提取釩的方法,其特征在于,所述方法包括以下步驟:(1)浸出:使用包含硫酸和助浸劑的酸性溶液對石煤粉進(jìn)行浸出,經(jīng)固液分離得到酸浸液;(2)黃鉀鐵礬法除雜:使步驟(1)得到的酸浸液在50~80℃保溫6~12h,期間ph控制為0.5~1.5,形成黃鐵礬沉淀,經(jīng)固液分離得到含釩凈化液;(3)中和氧化:將步驟(2)得到的含釩凈化液的ph值調(diào)節(jié)至1.5~2.5,再加入氧化劑將溶液中的低價釩氧化為五價釩,得到含釩清液;(4)離子交換吸附:使用離子交換樹脂吸附步驟(3)得到的含釩清液中的釩化合物;(5)離子交換解吸:使用解吸劑對步驟(4)中吸附后的離子交換樹脂進(jìn)行洗脫,得到富集了釩的洗脫液。2.如權(quán)利要求1所述的方法,其特征在于,所述方法具有以下一項或多項特征:步驟(1)中,石煤粉的粒度為40~100目;步驟(1)中,硫酸用量為石煤粉質(zhì)量的20~50%,助浸劑的用量為石煤粉質(zhì)量的1~5%,浸出體系的料液比為1:1~1:2;步驟(1)中,所述助浸劑為氯酸鈉和/或氯酸鉀;步驟(1)中,浸出溫度為80~100℃,浸出時間為6~24小時。3.如權(quán)利要求1所述的方法,其特征在于,步驟(1)還包括:將酸浸液的ph值調(diào)節(jié)至0.5~1.5,和/或?qū)⑺峤旱臏囟瓤刂茷?0~80℃。4.如權(quán)利要求1所述的方法,其特征在于,步驟(2)中,所述黃鐵礬包括黃鉀鐵礬和黃鈉鐵礬;和/或在保溫釜中進(jìn)行黃鐵礬的沉淀反應(yīng),所述保溫釜優(yōu)選具有加熱功能。5.如權(quán)利要求1所述的方法,其特征在于,所述方法具有以下一項或多項特征:步驟(3)中,添加堿性物質(zhì)調(diào)節(jié)含釩凈化液的ph至1.5~2.5,所述堿性物質(zhì)選自na2co3、nahco3和naoh中的一種或多種;步驟(3)中,加入的氧化劑為選自h2o2、naclo和naclo3中的一種或多種;步驟(3)中,氧化劑的添加量為將溶液中的低價釩氧化為五價釩所需的理論用量的1.2~2倍。6.如權(quán)利要求1所述的方法,其特征在于,步驟(4)中,使用大孔強堿性苯乙烯系陰離子交換樹脂進(jìn)行離子交換吸附;和/或?qū)⑽胶蟮奈菜糜诓襟E(1)中的浸出過程和/或用于洗滌步驟(1)中固液分離后的礦渣。7.如權(quán)利要求1所述的方法,其特征在于,步驟(5)中,使用質(zhì)量分?jǐn)?shù)為5~20%的naoh溶液作為解吸劑。8.如權(quán)利要求1所述的方法,其特征在于,所述方法還包括以下步驟:(6)沉釩:將步驟(5)得到的洗脫液中的釩以多釩酸銨的形式沉淀出來。9.如權(quán)利要求8所述的方法,其特征在于,所述沉釩為無氨沉釩,所述無氨沉釩包括:將洗脫液的ph調(diào)節(jié)至1.5~2.1后,加熱至80~100℃攪拌,使溶液中的釩以多釩酸銨的形式沉淀出來;優(yōu)選地,將沉釩尾水用于步驟(1)中的浸出過程。10.如權(quán)利要求8或9所述的方法,其特征在于,所述方法還包括以下步驟:(7)多釩酸銨熱解:對多釩酸銨加熱使之分解得到五氧化二釩。
技術(shù)總結(jié)
本發(fā)明公開了一種從石煤中提取釩的方法,所述方法包括以下步驟:(1)浸出:使用包含硫酸和助浸劑的酸性溶液對石煤粉進(jìn)行浸出,過濾得到酸浸液;(2)黃鉀鐵礬法除雜:使酸浸液在50~80℃保溫6~12h,期間pH控制為0.5~1.5,使用雜質(zhì)鐵以黃鐵礬的形式沉淀出來,過濾得到含釩凈化液;(3)中和氧化;(4)離子交換吸附;(5)離子交換解吸。本發(fā)明的方法釩的提取率高,避免中和過程出現(xiàn)的大量中和渣,縮短了流程,減少了物料消耗,保護環(huán)境,大幅降低了生產(chǎn)成本。大幅降低了生產(chǎn)成本。
技術(shù)研發(fā)人員:胡智敏
受保護的技術(shù)使用者:上海寰泰綠釩科技有限公司
技術(shù)研發(fā)日:2022.06.15
技術(shù)公布日:2022/9/6
聲明:
“從石煤中提取釩的方法與流程” 該技術(shù)專利(論文)所有權(quán)利歸屬于技術(shù)(論文)所有人。僅供學(xué)習(xí)研究,如用于商業(yè)用途,請聯(lián)系該技術(shù)所有人。
我是此專利(論文)的發(fā)明人(作者)