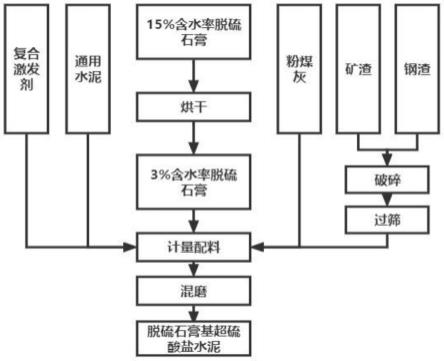
1.本發(fā)明屬于建筑材料技術(shù)領(lǐng)域,涉及一種超硫酸鹽水泥及其制備方法。
背景技術(shù):
2.要實現(xiàn)“雙碳”目標(biāo),應(yīng)著眼于co2的排放流程,而從源頭上減少co2排放是減排的重要一環(huán)。在建筑行業(yè)中,水泥材料一直是碳排放的“重災(zāi)區(qū)”,僅2020年碳排放量就達(dá)到了14.8億噸,而其中水泥產(chǎn)業(yè)的碳排放量更是達(dá)到了12.3億噸,占總排放量的83.11%,是“重災(zāi)區(qū)”中的“重災(zāi)區(qū)”。因此,降低現(xiàn)有普通硅酸鹽水泥的使用量是目前的主要解決方式之一。
3.降低生產(chǎn)水泥所產(chǎn)生高碳排放的技術(shù)路徑主要有兩種,一是降低混凝土中水泥的占比,即提高礦物摻合料或工業(yè)廢渣在水泥混凝土中的比例,二是使用可替代的新型低碳型膠凝材料。超硫酸鹽水泥是一種以?;郀t礦渣為主要原料,以石膏為硫酸鹽激發(fā)劑,配合堿性激發(fā)劑共同粉磨或分別粉磨而制成的少熟料或無熟料水硬性膠凝材料。超硫酸鹽水泥具有良好的使用性能,且生產(chǎn)工藝簡單、成本低,能充分利用工業(yè)副產(chǎn)物,屬于節(jié)能環(huán)保型水泥,符合國家可持續(xù)發(fā)展戰(zhàn)略。
4.cn113998969a公開了一種高硫型鋼渣
固廢膠凝材料及其制備方法,該超硫酸鹽水泥的組成按重量級包括:鋼渣35%~45%、礦渣25%~35%、粉煤灰 0%~15%、副產(chǎn)石膏10%~15%、水泥10%~15%,該固廢基膠凝材料無任何外加堿性激發(fā)劑,同時后期強度高,體積穩(wěn)定性良好,雖然試件可以1d成型,但是并未解決早期強度較低的問題,無法滿足技術(shù)需求。
5.cn 113372029a公開了一種低碳型超硫酸鹽水泥及其制備方法,以及水泥砂漿,該超硫酸鹽水泥的組成按重量級包括:鈦石膏10%~40%、水泥熟料15%~30%、礦渣粉20%~40%、鋼渣5%~10%、提鈦尾渣5%~10%、釩渣1%~5%、粉煤灰2%~10%、激發(fā)劑0.5%~1%、減水劑0.5%~1%。所述超硫酸鹽水泥熟料摻量依舊較大且大量利用了鈦石膏,該種石膏含水率高,雜質(zhì)較多,穩(wěn)定性能需要較為復(fù)雜的除雜工藝。
6.cn113277759a公開了一種鈦礦渣基固廢膠凝材料及其制備方法,按重量百分比計,包括以下原料:鈦礦渣基材料70%~80%、石膏15%~25%、水泥熟料 2.5%~7.5%,制備方法簡單。該超硫酸鹽水泥不能在常溫20℃的條件下提高早期強度,只能采用高溫蒸養(yǎng)的方式加速水化,成本高,規(guī)?;茝V應(yīng)用難。
7.cn 101423343a公開了一種鋼渣超硫酸鹽水泥及其制備方法,該超硫酸鹽水泥的組成按重量級包括鋼渣20%~80%、礦渣和/或粉煤灰5%~65%、硫酸鹽激活劑5%~25%、水泥熟料或氫氧化鈣1%~10%以及堿性激活劑0.05%~3%,該超硫酸鹽水泥的最主要組分為鋼渣,鋼渣的水化活性不佳,且與其他組分的粘結(jié)性較弱,造成力學(xué)性能較差,不能滿足《gb 175-2020通用硅酸鹽水泥》規(guī)范要求。
8.cn 111302677a提供了一種超硫酸鹽水泥及其制備方法,所述超硫酸鹽水泥按質(zhì)量分?jǐn)?shù)計,包括以下組分:第一礦渣40%~60%、第二礦渣10%~30%、通用水泥2%~8%、
石膏10%~25%、堿性激發(fā)劑0.5%~2%、石灰石3%~10%,其中,所述第一礦渣和第二礦渣的粒徑分布不同。所述超硫酸鹽水泥通過將礦渣原料粒徑分級化,提高超硫酸鹽水泥的密實度,進(jìn)一步提高抗碳化性能。但其所用石膏主要為天然石膏,現(xiàn)在已禁止開采,成本較高。
9.cn 111205002a涉及一種高韌性超硫酸鹽水泥及其制備方法,主要是克服現(xiàn)有技術(shù)中的不足之處,提出一種高強、高韌性、高耐久的高韌性超硫酸鹽水泥及其制備方法,包括以下重量百分比的組分:礦渣65~90%、石膏10~25%、激發(fā)劑1~15%、摻合料1~10%、纖維0~3%、調(diào)凝型減水劑0~1%。此發(fā)明制備的高韌性超硫酸鹽水泥從一定程度上改善了抗硫酸鹽侵蝕能力、抗彎撓度和收縮率。但此發(fā)明中石膏需要5次水洗,140℃煅燒4h,還需要石灰中和,陳化 72h,耗水、耗能,流程較長,成本較高。
10.現(xiàn)有專利技術(shù)中將脫硫石膏引入超硫酸鹽水泥中的研究較少。脫硫石膏是由燃煤電廠進(jìn)行濕法石灰/石灰石―石膏法脫硫而產(chǎn)生的以caso4·
2h2o為主要成分的工業(yè)副產(chǎn)物,僅2019年,我國脫硫石膏產(chǎn)量就達(dá)到了71.5mt,現(xiàn)階段,我國脫硫石膏的綜合利用途徑比較單一,大量的脫硫石膏不僅占用土地資源,其含有的酸根、重金屬等污染物還會對空氣、水體和土壤產(chǎn)生巨大的污染。脫硫石膏和天然石膏相比,脫硫石膏具有顆粒均勻、比表面積大、成分相近、純度較高等優(yōu)點,開展脫硫石膏資源綜合利用的研究具有重要的經(jīng)濟(jì)意義和社會意義。
技術(shù)實現(xiàn)要素:
11.本發(fā)明的目的在于提供一種脫硫石膏基超硫酸鹽水泥及其制備方法,從根本上解決了現(xiàn)有專利中材料早期強度低,強度提升慢的問題,并通過調(diào)整配合比使產(chǎn)品形成po 32.5、po 42.5、po 52.5的強度梯度以適用于不同工程場景。本發(fā)明提供的脫硫石膏基超硫酸鹽水泥能夠大量利用脫硫石膏及其他工業(yè)廢渣、降低工業(yè)廢棄物對環(huán)境的污染,同時能夠提高早期力學(xué)性能、保障后期強度,生產(chǎn)工藝簡單,性能穩(wěn)定,各項強度指標(biāo)均符合《gb175-2020通用水泥規(guī)范》規(guī)范要求,復(fù)合激發(fā)劑用量小且不需要外摻減水劑,經(jīng)濟(jì)性較好,具有廣闊的推廣前景。
12.本發(fā)明提供了一種脫硫石膏基超硫酸鹽水泥,包括以下質(zhì)量比的組分:
[0013][0014]
優(yōu)選的,所述脫硫石膏均為二水石膏。
[0015]
優(yōu)選的,所述脫硫石膏的含水量≤15wt%。
[0016]
優(yōu)選的,所述激發(fā)劑為復(fù)合激發(fā)劑;
[0017]
優(yōu)選的,所述復(fù)合激發(fā)劑的各組分按質(zhì)量比計為;堿性激發(fā)劑60%~90%,鋁酸鹽
激發(fā)劑10%~40%;
[0018]
優(yōu)選的,堿性激發(fā)劑為硅酸鈉,鋁酸鹽激發(fā)劑為鋁酸鈣。
[0019]
優(yōu)選的,所述鋼渣的粒度在100目以下。
[0020]
優(yōu)選的,所述礦渣粉為s95礦渣粉;
[0021]
優(yōu)選的,所述礦渣粉的比表面積為300~500m2/kg,例如300m2/kg、320m2/kg、 350m2/kg、375m2/kg、400m2/kg、420m2/kg、450m2/kg、480m2/kg或500m2/kg 等。
[0022]
本發(fā)明采用脫硫石膏、鋼渣等工業(yè)固廢與通用水泥、礦渣粉、粉煤灰、復(fù)合激發(fā)劑以一定比例搭配,其中,脫硫石膏的用量在20%以上,其它渣料的用量在30%以上,大量利用了脫硫石膏及其他工業(yè)廢渣、降低工業(yè)廢棄物對環(huán)境的污染,同時還能夠顯著提升材料的早期力學(xué)性能(即3d強度)及標(biāo)準(zhǔn)齡期力學(xué)性能(28d強度),可以依據(jù)《gb175-2020通用水泥規(guī)范》按照po 32.5、po 42.5、 po 52.5的強度等級對脫硫石膏基超硫酸鹽水泥進(jìn)行分級,以保障本發(fā)明可以用于不同工程場景。
[0023]
實驗結(jié)果表明,本發(fā)明提供的脫硫石膏基超硫酸鹽水泥膠砂在標(biāo)準(zhǔn)養(yǎng)護(hù)條件下,3d抗折強度可以達(dá)到4.5mpa以上,3d抗壓強度達(dá)到22mpa以上;28d 抗折強度達(dá)到9mpa以上,28d抗壓強度達(dá)到60mpa以上。
[0024]
本發(fā)明的有益效果:
[0025]
(1)本發(fā)明以高爐礦渣、脫硫石膏為主要原料,寧夏地區(qū)此兩種原料來源豐富,產(chǎn)量大,原材料成本低。
[0026]
(2)本發(fā)明的原材料中,高爐礦渣和脫硫石膏屬于工業(yè)廢渣,對工業(yè)廢渣的再利用,創(chuàng)造經(jīng)濟(jì)價值的同時,又節(jié)能環(huán)保。
[0027]
(3)本發(fā)明進(jìn)一步簡化制備工藝,原材料自身純度較高,不需要復(fù)雜的除雜工藝,晾干混磨即可。
[0028]
(4)本發(fā)明所述的脫硫石膏基超硫酸鹽水泥3d抗壓強度可以達(dá)到22mpa 以上,性能穩(wěn)定、可控。各種技術(shù)參數(shù)均符合《gb175-2020通用水泥規(guī)范》要求。
附圖說明
[0029]
為了更清楚地說明本發(fā)明的實施方式或現(xiàn)有技術(shù)中的技術(shù)方案,下面將對實施方式中所需要使用的附圖作簡單地介紹。顯而易見地,下面描述中的附圖僅僅是示例性的,對于本領(lǐng)域普通技術(shù)人員來講,在不付出創(chuàng)造性勞動的前提下,還可以根據(jù)提供的附圖延伸獲得其他的實施附圖。圖1為本發(fā)明實施例制備脫硫石膏基超硫酸鹽水泥的流程示意圖。
具體實施方式
[0030]
本發(fā)明提供了一種脫硫石膏基超硫酸鹽水泥,包括以下質(zhì)量比的組分:
[0031][0032]
本發(fā)明采用脫硫石膏、鋼渣等工業(yè)固廢與通用水泥、礦渣粉、粉煤灰、復(fù)合激發(fā)劑以一定比例搭配,其中,脫硫石膏的用量在20%以上,其它渣料的用量在30%以上,大量利用了脫硫石膏及其他工業(yè)廢渣、降低工業(yè)廢棄物對環(huán)境的污染,同時還能夠顯著提升材料的早期力學(xué)性能(即3d強度)及標(biāo)準(zhǔn)齡期力學(xué)性能(28d強度)。
[0033]
脫硫石膏是由燃煤電廠進(jìn)行濕法石灰/石灰石―石膏法脫硫而產(chǎn)生的工業(yè)副產(chǎn)物。本發(fā)明中,所述脫硫石膏優(yōu)選為經(jīng)過預(yù)處理的脫硫石膏;所述預(yù)處理包括:干燥、磨制和篩選。本發(fā)明通過干燥控制脫硫石膏含水量≤5wt%。通過磨制及篩選控制脫硫石膏的粒度在100目以下,即控制粉體的粒度≤100目篩對應(yīng)的粒度,100目篩對應(yīng)的粒度為150μm,即控制脫硫石膏的粒度≤150μm。篩子的目數(shù)越大,對應(yīng)的粉體粒度越小,本發(fā)明中控制脫硫石膏的粒度在100目以下,即篩子的目數(shù)在100目以上。更優(yōu)選的,所述脫硫石膏的粒度為100~120 μm。
[0034]
本發(fā)明中,所述脫硫石膏在原料中的質(zhì)量比為10%~40%。水泥中脫硫石膏等廢渣的添加量越高,越容易影響材料的力學(xué)性能,現(xiàn)有技術(shù)中水泥配料即使引入脫硫石膏,通常用量在5%以下,最多到10%且需要進(jìn)行復(fù)雜的處理(如水洗、煅燒、中和、陳化等),而本發(fā)明中,通過各種組分的選擇與調(diào)配,能夠使脫硫石膏的添加量達(dá)到10%以上且無需對脫硫石膏進(jìn)行復(fù)雜特殊的預(yù)處理、僅進(jìn)行干燥及磨制的簡單處理即可,大大提升了脫硫石膏的利用率,減少了固廢物的環(huán)保壓力和治理壓力。在本發(fā)明的一些實施例中,脫硫石膏的用量為20%、 30%或40%。
[0035]
本發(fā)明中,所述通用水泥優(yōu)選為po 42.5。本發(fā)明對所述通用水泥的來源沒有特殊限制,為一般市售品即可。本發(fā)明中,所述通用水泥的粒度在100目以下。粉體粒度與篩子目數(shù)的對應(yīng)關(guān)系與前文所述一致,即控制通用水泥的粒度≤150μm,更優(yōu)選為100~120μm。本發(fā)明中,所述通用水泥在原料中的質(zhì)量比為1%~10%;在本發(fā)明的一些實施例中,所述質(zhì)量比為5%或10%。
[0036]
本發(fā)明中,所述礦渣粉優(yōu)選為國家標(biāo)準(zhǔn)s95礦渣粉。本發(fā)明對所述礦渣粉的來源要求為鋼鐵廠排出的粒化高爐礦渣經(jīng)球磨或立磨加工所得的市售品。本發(fā)明中,所述礦渣粉的比表面積在400m2/kg以上。本發(fā)明中,所述礦渣粉在原料中的質(zhì)量比為30%~60%;在本發(fā)明的一些實施例中,所述質(zhì)量比為40%、 50%或60%。
[0037]
本發(fā)明中,所述鋼渣在使用前優(yōu)選進(jìn)行破碎和篩分。本發(fā)明中,所述鋼渣的粒度在100目以下。粉體粒度與篩子目數(shù)的對應(yīng)關(guān)系與前文所述一致,即控制鋼渣的粒度≤150μm,更優(yōu)選為100~120μm。本發(fā)明中,所述鋼渣在原料中的質(zhì)量比為5%~30%;在本發(fā)明的一些實施例中,所述質(zhì)量比為20%或30%。
[0038]
本發(fā)明中,所述粉煤灰的粒度優(yōu)選細(xì)度8~12的一級灰。本發(fā)明中,所述粉煤灰在原料中的質(zhì)量比為5%~30%;在本發(fā)明的一些實施例中,所述質(zhì)量比為 20%或30%。
[0039]
本發(fā)明中,所述復(fù)合激發(fā)劑優(yōu)選為堿性激發(fā)劑和鋁酸鹽激發(fā)劑進(jìn)行復(fù)合,其中堿性激發(fā)劑60%~90%,鋁酸鹽激發(fā)劑10%~40%。本發(fā)明中,堿性激發(fā)劑優(yōu)選為氫氧化鈉,鋁酸鹽激發(fā)劑優(yōu)選為鋁酸鈣。本發(fā)明中,所述復(fù)合激發(fā)劑在原料中的質(zhì)量比為1%~10%;在本發(fā)明的一些實施例中,所述質(zhì)量比為10%。
[0040]
本發(fā)明還提供了一種上述技術(shù)方案中所述的脫硫石膏基超硫酸鹽水泥的制備方法,包括:
[0041]
將脫硫石膏、通用水泥、礦渣粉、鋼渣、粉煤灰、復(fù)合激發(fā)劑混合球磨,得到脫硫石膏基超硫酸鹽水泥。
[0042]
其中,各種原料的種類及用量等均與上述技術(shù)方案中所述一致,在此不再一一贅述。
[0043]
本發(fā)明提供的脫硫石膏基超硫酸鹽水泥,采用脫硫石膏、通用水泥、礦渣粉、鋼渣、粉煤灰、復(fù)合激發(fā)劑以一定比例搭配形成上述脫硫石膏基超硫酸鹽水泥,其水化機理及水化產(chǎn)物與普通硅酸鹽水泥均有所不同。普通硅酸鹽水泥的主要水化產(chǎn)物為硅酸三鈣、硅酸二鈣、鋁酸三鈣、鐵鋁酸四鈣、氫氧化鈣。超硫酸鹽水泥是以堿和硫酸鹽共同激發(fā)礦渣,水化放熱低,其主要水化產(chǎn)物為水化硅酸鈣凝膠及二水硫酸鈣晶體,具有較好的耐久性,尤其是抗硫酸鹽侵蝕性優(yōu)異,可適用于大體積混凝土工程、道路混凝土工程以及硫酸鹽侵蝕環(huán)境混凝土工程。
[0044]
本發(fā)明通過上述配方設(shè)計,采用上述特定原料以一定比例搭配,在大量利用脫硫石膏及其他工業(yè)廢渣的情況下,還能夠提升材料的早期力學(xué)性能(即3d 強度),標(biāo)準(zhǔn)齡期力學(xué)性能(即28d強度)?,F(xiàn)有技術(shù)中的脫硫石膏綜合利用手段單一,作水泥緩凝劑摻入量有限,附加值低;而本發(fā)明使用脫硫石膏生產(chǎn)超硫酸鹽水泥并用于水泥穩(wěn)定碎石技術(shù)有望實現(xiàn)大量消解脫硫石膏和高爐礦渣,實現(xiàn)建設(shè)綠色道路的目的,擁有廣闊的市場空間。
[0045]
為了進(jìn)一步理解本發(fā)明,下面結(jié)合實施例對本發(fā)明優(yōu)選實施方案進(jìn)行描述,但是應(yīng)當(dāng)理解,這些描述只是為進(jìn)一步說明本發(fā)明的特征和優(yōu)點,而不是對本發(fā)明權(quán)利要求的限制。
[0046]
以下實施例中,脫硫石膏取自寧夏寶豐集團(tuán);通用水泥牌號為po 42.5,購自寧夏賽馬水泥廠;礦粉為s95礦粉,購自寧夏悅筑有限公司;粉煤灰為一級灰,取自寧夏大武口電廠;鋼渣取自寧夏建龍鋼廠。
[0047]
以下實施例中,各原料的主要成分參見表1。
[0048]
表1原料的主要成分
[0049]
成分,wt%al2o3sio2so3caofe2o3mgo礦渣粉13.8828.343.4043.140.496.85脫硫石膏0.612.2442.2351.040.381.76鋼渣2.0613.990.3034.4232.225.28粉煤灰22.7635.433.298.115.574.01
[0050] 實施案例一:po 32.5緩凝型脫硫石膏基超硫酸鹽水泥
[0051]
目前公路工程水穩(wěn)基層用到的水泥大多為緩凝水泥,為了實現(xiàn)規(guī)?;瘧?yīng)用,本發(fā)
明專利提供了一種po 32.5緩凝型脫硫石膏基超硫酸鹽水泥。
[0052]
參照圖1進(jìn)行原料處理和制備脫硫石膏基超硫酸鹽水泥,圖1為本發(fā)明實施例制備脫硫石膏基超硫酸鹽水泥的流程示意圖。
[0053]
1、原料處理:
[0054]
將脫硫石膏干燥,得到含水量5wt%的脫硫石膏。
[0055]
將鋼渣球磨并過200目篩,得到200目粉料。
[0056]
將礦渣球磨并過100目篩,得到100目礦粉。
[0057]
2、水泥原料配方:
[0058]
脫硫石膏30~40%,通用水泥1~5%,礦渣粉15~25%,鋼渣1~5%,粉煤灰20~30%,復(fù)合激發(fā)劑1~5%,1~3
‰
糖類緩凝劑?;炷ヅ淞希簩⑸鲜鲈戏湃肭蚰C,球磨介質(zhì)為不銹鋼,球料比為1.0,于轉(zhuǎn)速300r/min下球磨1h,得到脫硫石膏基超硫酸鹽水泥料。各技術(shù)參數(shù)見表3。
[0059]
3、制備水泥膠砂:
[0060]
參照國標(biāo)《gb/t 175-2008水泥膠砂強度檢驗方法》的方法將脫硫石膏基超硫酸鹽水泥料與水、標(biāo)準(zhǔn)砂混合攪拌,裝入模具,養(yǎng)護(hù)并檢測其抗折強度和抗壓強度。
[0061]
其中,制備水泥膠砂的過程如下:
[0062]
按照標(biāo)準(zhǔn)砂與水泥料質(zhì)量比3.0配料,并按水與配料質(zhì)量比0.5加入水,在 jj-5型膠砂攪拌機中攪拌均勻后,裝入模具,在zs-15型膠砂振動臺振動均勻后得到脫硫石膏基水泥膠砂。所得膠砂試塊強度見表2。
[0063]
4、制備水泥穩(wěn)定碎石:
[0064]
參照行標(biāo)《jtg e51-2009公路工程無機結(jié)合料穩(wěn)定材料試驗規(guī)程》的方法將脫硫石膏基超硫酸鹽水泥與集料、水混合測試無側(cè)限抗壓強度,按照先后順序包括以下步驟:
[0065]
步驟一:設(shè)計一種骨料密實型的水泥穩(wěn)定碎石級配,級配石灰石粒徑分布為:細(xì)集料的含量為35%,粗集料的含量為65%,其中,4.75mm篩孔通過率為35%,9.5mm篩孔通過率為55%,19mm篩孔通過率80%,25mm篩孔通過率為100%;
[0066]
步驟二:將5.5kg的級配碎石及2%級配碎石質(zhì)量的外摻水置于封口塑料袋內(nèi)浸潤24h備用;
[0067]
步驟三:將浸潤完全的試料倒入拌和鍋并加入2.8%級配碎石質(zhì)量的外摻水拌合30s;
[0068]
步驟四:在拌和鍋中加入脫硫石膏基超硫酸鹽水泥,摻量為5%配碎石質(zhì)量,拌合90s;
[0069]
步驟五:將水泥穩(wěn)定碎石擊實后在25℃,95%相對濕度的環(huán)境下根據(jù)需求養(yǎng)生至相應(yīng)齡期,(實驗室條件下需在25℃,95%相對濕度的環(huán)境中放置8小時后脫模)。
[0070]
所得脫硫石膏基超硫酸鹽水泥穩(wěn)定碎石7d無側(cè)限抗壓強度為5.90mpa,28d 無側(cè)線抗壓強度為7.85mpa,符合行標(biāo)《jtg/t f20—2015公路路面基層施工技術(shù)細(xì)則》重交通要求。
[0071]
實施案例二:po 42.5型脫硫石膏基超硫酸鹽水泥
[0072]
為了拓寬應(yīng)用場景,提高脫硫石膏基超硫酸鹽水泥利用率,本發(fā)明專利提供了一種po 42.5型脫硫石膏基超硫酸鹽水泥,該水泥可以用于附屬工程和預(yù)制構(gòu)件。
[0073]
1、原料處理:同實施例1。
[0074]
2、水泥原料配方:
[0075]
脫硫石膏20~30%,通用水泥5~10%,礦渣粉25~35%,鋼渣15~25%,粉煤灰5~10%,復(fù)合激發(fā)劑1~5%。混磨配料:同實施例1。各技術(shù)參數(shù)見表3。
[0076]
3、制備水泥砂漿:同實施例1。
[0077]
4、按照c40制備水泥混凝土;參照行標(biāo)《jgj 55-2011普通混凝土配合比設(shè)計規(guī)程》的方法將脫硫石膏基超硫酸鹽水泥與集料、水混合測試抗壓、抗折強度,按照先后順序包括以下步驟:
[0078]
步驟一:配料,按照c40混凝土配合比將脫硫石膏基超硫酸鹽水泥與集料、水通過攪拌釜拌和均勻而得到拌和料;
[0079]
步驟二:產(chǎn)品成型;
[0080]
步驟三:養(yǎng)護(hù),養(yǎng)護(hù)工藝包括蒸汽養(yǎng)護(hù)和自然養(yǎng)護(hù)。
[0081]
所得脫硫石膏基超硫酸鹽水泥混凝土7d抗壓強度為24.7mpa,抗折強度3.3mpa;28d抗壓強度為45.2mpa,抗折強度5.2mpa,符合國標(biāo)《gb/t50107-2010 混凝土強度檢驗評定標(biāo)準(zhǔn)》要求。
[0082]
實施案例三:po 52.5型脫硫石膏基超硫酸鹽水泥
[0083]
為了滿足部分場景要求,本發(fā)明專利提供了一種po 52.5型脫硫石膏基超硫酸鹽水泥,該水泥可以用于高強等級混凝土、快速修補工程。
[0084]
1、原料處理:同實施例1。
[0085]
2、水泥原料配方:
[0086]
脫硫石膏20~30%,通用水泥5~10%,礦渣粉35~45%,鋼渣10~20%,粉煤灰1~5%,復(fù)合激發(fā)劑5~10%?;炷ヅ淞希和瑢嵤├?。各技術(shù)參數(shù)見表3。
[0087]
3、制備水泥砂漿:同實施例1。
[0088]
4、按照c50制備水泥混凝土;其它同實例2。
[0089]
所得脫硫石膏基超硫酸鹽水泥混凝土7d抗壓強度為27.9mpa,抗折強度 4.4mpa;28d抗壓強度為57.3mpa,抗折強度7.9mpa,符合國標(biāo)《gb/t50107-2010 混凝土強度檢驗評定標(biāo)準(zhǔn)》要求。
[0090]
表2實施例1~3所得水泥膠砂試塊的性能
[0091] 抗折強度,mpa抗折強度,mpa抗壓強度,mpa抗壓強度,mpa 3d28d3d28d實例13.35.714.436.6實例24.37.817.846.4實例35.18.522.667.9
[0092] 表3實施例1~3所得水泥技術(shù)參數(shù)
[0093][0094]
由表2和表3測試結(jié)果可知,通過提高石膏和粉煤灰摻量,可以有效地提高凝結(jié)時間,在符合325水泥強度要求的基礎(chǔ)上進(jìn)一步滿足道路基層工程用需要。實施例2中通過降低脫硫石膏摻量,提高鋼渣摻量,在降低凝結(jié)時間的同時,提高了早期強度,使產(chǎn)品成型更快,強度更高。實施例3中進(jìn)一步提高了礦渣摻量,同時調(diào)整了復(fù)合激發(fā)劑含量,與實施例1相比,28d抗壓強度提高更為明顯,初凝時間的大幅度縮短也使其可以應(yīng)用于快速修補工程。實例1~3的各項技術(shù)指標(biāo)均符合規(guī)范要求,性能較為穩(wěn)定。
[0095]
本文中應(yīng)用了具體個例對本發(fā)明的原理及實施方式進(jìn)行了闡述,以上實施例的說明只是用于幫助理解本發(fā)明的方法及其核心思想,包括最佳方式,并且也使得本領(lǐng)域的任何技術(shù)人員都能夠?qū)嵺`本發(fā)明,包括制造和使用任何裝置或系統(tǒng),和實施任何結(jié)合的方法。應(yīng)當(dāng)指出,對于本技術(shù)領(lǐng)域的普通技術(shù)人員來說,在不脫離本發(fā)明原理的前提下,還可以對本發(fā)明進(jìn)行若干改進(jìn)和修飾,這些改進(jìn)和修飾也落入本發(fā)明權(quán)利要求的保護(hù)范圍內(nèi)。本發(fā)明專利保護(hù)的范圍通過權(quán)利要求來限定,并可包括本領(lǐng)域技術(shù)人員能夠想到的其他實施例。如果這些其他實施例具有近似于權(quán)利要求文字表述的結(jié)構(gòu)要素,或者如果它們包括與權(quán)利要求的文字表述無實質(zhì)差異的等同結(jié)構(gòu)要素,那么這些其他實施例也應(yīng)包含在權(quán)利要求的范圍內(nèi)。技術(shù)特征:
1.一種脫硫石膏基超硫酸鹽水泥及其制備方法,其特征在于,包括以下質(zhì)量比的組分:2.根據(jù)權(quán)利要求1所述的脫硫石膏基超硫酸鹽水泥,其特征在于,所述脫硫石膏均為二水石膏。3.根據(jù)權(quán)利要求1所述的脫硫石膏基超硫酸鹽水泥,其特征在于,所述脫硫石膏的含水量≤15wt%。所述脫硫石膏的比表面積為300~500m2/kg。4.根據(jù)權(quán)利要求1所述的脫硫石膏基超硫酸鹽水泥,其特征在于,所述復(fù)合激發(fā)劑由堿性激發(fā)劑、鋁酸鹽激發(fā)劑組成。所述復(fù)合激發(fā)劑的各組分按質(zhì)量比計為;堿性激發(fā)劑60%~90%,鋁酸鹽激發(fā)劑10%~40%。5.根據(jù)權(quán)利要求1或4所述的脫硫石膏基超硫酸鹽水泥,其特征在于,所述堿性激發(fā)劑至少一種選自于硅酸鈉、氫氧化鈉、或碳酸鈉。6.根據(jù)權(quán)利要求1或4所述的脫硫石膏基超硫酸鹽水泥,其特征在于,所述鋁酸鹽激發(fā)劑至少一種選自于鋁礬土、鋁酸鈉、或鋁酸鈣。7.根據(jù)權(quán)利要求1所述的脫硫石膏基超硫酸鹽水泥,其特征在于,所述礦渣粉均為高爐礦渣;所述高爐礦渣的來源包括鋼鐵廠排出的?;郀t礦渣;所述礦渣粉的比表面積為400~500m2/kg;所述礦粉為s95礦渣粉。8.根據(jù)權(quán)利要求1所述的脫硫石膏基超硫酸鹽水泥,其特征在于,所述粉煤灰為電廠產(chǎn)一級灰。9.根據(jù)權(quán)利要求1所述的脫硫石膏基超硫酸鹽水泥,其特征在于,所述通用水泥包括硅酸鹽水泥和/或普通硅酸鹽水泥。10.根據(jù)權(quán)利要求1所述的脫硫石膏基超硫酸鹽水泥,其特征在于,所述鋼渣的粒度在100目以下。11.一種權(quán)利要求1~10中任一項所述的脫硫石膏基超硫酸鹽水泥的制備方法,其特征在于,包括:將脫硫石膏、通用水泥、礦渣粉、鋼渣、粉煤灰、復(fù)合激發(fā)劑混合球磨,得到脫硫石膏基超硫酸鹽水泥。12.根據(jù)權(quán)利要求11所述的制備方法,其特征在于,所述組分在混合前先各自進(jìn)行粉磨
以達(dá)到粒徑要求。
技術(shù)總結(jié)
本發(fā)明提供了一種脫硫石膏基超硫酸鹽水泥及其制備方法。本發(fā)明提供的脫硫石膏基超硫酸鹽水泥,包括以下質(zhì)量比的組分:脫硫石膏10%~40%、通用水泥1%~10%、礦渣粉30%~60%、鋼渣5%~30%、粉煤灰5%~30%、復(fù)合激發(fā)劑1%~10%。本發(fā)明采用脫硫石膏、鋼渣、高爐礦渣、粉煤灰等工業(yè)固廢與水泥熟料、復(fù)合激發(fā)劑以一定比例搭配,其中,脫硫石膏的用量在20%以上,大量利用了脫硫石膏及其他工業(yè)廢渣、降低了工業(yè)廢棄物對環(huán)境的污染,同時顯著提升了材料的早期力學(xué)性能,還通過調(diào)整配比形成強度梯度使其可以應(yīng)用于不同工程場景。成強度梯度使其可以應(yīng)用于不同工程場景。成強度梯度使其可以應(yīng)用于不同工程場景。
技術(shù)研發(fā)人員:張志濤 賈小龍 陳浩旭 門光譽 惠迎新 馮玉釧 萬磊 楊洋 虎占輝 張偉
受保護(hù)的技術(shù)使用者:寧夏交建交通科技研究院有限公司 寧夏嘉惠道路資源再生利用有限公司
技術(shù)研發(fā)日:2022.05.20
技術(shù)公布日:2022/7/12 一種鈦鐵礦的冶煉新工藝的制作方法
【專利摘要】一種鈦鐵礦的冶煉新工藝,是一種金屬冶煉技術(shù),尤其是一種在鈦鐵礦的冶煉新工藝。該工藝是將破碎的鈦鐵礦進(jìn)入電爐中進(jìn)行冶煉,然后出料,渣鐵分離并獲得高鈦渣,其特征在于該鈦鐵礦在進(jìn)電爐冶煉前首先進(jìn)行預(yù)還原處理,其具體冶煉過程是:首先,將破碎后與含碳物料混合的鈦鐵礦壓制成塊狀;第二,將壓制成塊的鈦鐵礦在真空爐窯中進(jìn)行堆垛焙燒;第三,焙燒完成后冷卻出爐;最后,將出爐的鈦鐵礦投入電爐中冶煉。本發(fā)明工藝不僅節(jié)能環(huán)保,還能避免出現(xiàn)電爐中的物料塌料和翻渣現(xiàn)象,保障生產(chǎn)人員的生產(chǎn)安全。
【專利說明】一種鈦鐵礦的冶煉新工藝
【技術(shù)領(lǐng)域】
[0001]本發(fā)明是一種金屬冶煉技術(shù),尤其是一種在鈦鐵礦的冶煉新工藝?!颈尘凹夹g(shù)】 鈦是一種化學(xué)元盡,化學(xué)符號Ti,原子序數(shù)22,是一種銀白色的過渡金屬。鈦的密度為
4.506-4.516克/立方厘米(20°C),高于鋁而低于鐵、銅、鎳,佰比強度位于金屬之首。熔點1668±4°C。欽具有可塑件,高鈍鈦的延伸率可汰50-60%,斷面收縮率可達(dá)70_80%。
[0002]鈦具有熔點高、比重小、比強度高、韌性好、抗疲勞、耐腐蝕、導(dǎo)熱系數(shù)低、高低溫度耐受性能好、在急冷急熱條件下應(yīng)力小等特點,被應(yīng)用于航空、航天等高科技領(lǐng)域,并不斷向化工、石油、電力、海水淡化、建筑、日常生活用品等行業(yè)推廣,
鈦金屬日益被人們重視,被譽為“現(xiàn)代金屬”和“
戰(zhàn)略金屬”,是提高國防裝備水平不可或缺的重要戰(zhàn)略物資,也是衡量一個國家工業(yè)規(guī)模的重要指標(biāo)。
[0003]在地殼中,鈦的儲量僅次于鐵、鋁、鎂,居第四位,中國鈦資源總量9.65億噸,居世界之首,占世界探明儲量的38.85%,主要集中在_、云南、亡東、廣西及迤直等地。鈦的主要礦石是金紅石TiO2、鈦鐵礦FeTiO3和
鈣鈦礦,存在分散難以提取。
[0004]制取金屬鈦的原料主要為金紅石和鈦鐵礦FeTiO3,金紅石中含TiO2大于96%。缺少金紅石礦的國家則采用鈦鐵礦制成高鈦渣,其中含TiO2在90%左右。因天然金紅石漲價和儲量日減,各國都趨向于用鈦鐵礦制成富鈦料,即高鈦渣和人造金紅石來制取金屬鈦。工業(yè)上常用硫酸分解鈦鐵礦的方法制取二氧化鈦,再由二氧化鈦制取金屬鈦。
[0005]電爐法是目前工業(yè)上鈦鐵礦制取富鈦料的一種高效方法,該方法采用碳作為還原劑,對鈦鐵礦進(jìn)行微波碳熱還原,以獲得TiO2,但存在生產(chǎn)成本高、耗能大等問題。
[0006]以云南富民產(chǎn)鈦鐵礦冶煉為列,該鈦鐵礦中含TiO2約42~46%,F(xiàn)e約31~35%,采用自焙電極敞口式的電爐冶煉熔煉高鈦渣,TiO2含量可達(dá)到72、2%以上。其具體的冶煉工藝是將鈦鐵礦破碎后與焦煤或木炭等含碳物料混合配料,并進(jìn)入電爐中進(jìn)行冶煉,然后出料渣鐵分離,破碎篩分,經(jīng)磁選有形成高鈦渣。該方法中主要涉及的反應(yīng)式為:
FeTi03+C=Fe+Ti02+C0 ;
FeTi03+C0=Fe+Ti02+C02 ;
C02+C=2C0 ;
常見的電爐,其額定容量6300kVA,一次可冶煉鈦鐵礦20噸,電爐電耗量在6300kw.h,在冶煉TiO2含量大于92%的高鈦渣時,需要冶煉6小時出渣,按一度電0.5元計算,電力費用在18900元,其耗電量相當(dāng)大。與此同時,敞口式電爐冶煉還會存在塌料和翻渣的情況,導(dǎo)致電壓電流的不穩(wěn)定,造成熱料四處噴濺導(dǎo)致發(fā)生加料人員灼燙事故,冶煉過程環(huán)境
亞少
[0007]目前,為實現(xiàn)鈦鐵礦電爐法高效低耗的制備富鈦料,對電爐法制備高鈦渣技術(shù)進(jìn)行了多方面的優(yōu)化研究,提出低溫還原鈦鐵礦生產(chǎn)高鈦渣的方法,發(fā)現(xiàn)了在760 °C條件下恒溫30 min基本上將鐵從鈦精礦中還原出來這一低溫反應(yīng)現(xiàn)象,但是要實現(xiàn)該工藝需要鈦精礦的顆粒度在廣2 um,一般球磨機難以實現(xiàn)這一目標(biāo),即使能夠達(dá)到,也將耗費大量能量,因此無法實現(xiàn)規(guī)?;墓I(yè)應(yīng)用。
【發(fā)明內(nèi)容】
[0008]本發(fā)明的目的就是解決目前采用自焙電極敞口式的電爐冶煉熔煉高鈦渣低效高耗能的問題,提出一種鈦鐵礦的冶煉新工藝,該工藝能夠降低生產(chǎn)成本,提高電能利用率,并保證高鈦渣的質(zhì)量,使其符合相關(guān)國家標(biāo)準(zhǔn)要求。
[0009]本發(fā)明的一種鈦鐵礦的冶煉新工藝,該工藝是將破碎的鈦鐵礦進(jìn)入電爐中進(jìn)行冶煉,然后出料,渣鐵分離并獲得高鈦渣,其特征在于該鈦鐵礦在進(jìn)電爐冶煉前首先進(jìn)行預(yù)還原處理,其具體冶煉過程是:
首先,將破碎后與含碳物料混合的鈦鐵礦壓制成塊狀;
第二,將壓制成塊的鈦鐵礦在真空爐窯中進(jìn)行堆垛焙燒; 第三,焙燒完成后冷卻出爐;
最后,將出爐的鈦鐵礦投入電爐中冶煉。
[0010]其中,所述的含碳物料為焦煤,按重量份,鈦鐵礦:含碳物料=1:0.08、.12的比例進(jìn)行混料。鈦鐵礦的微波還原速率與物料中含碳量關(guān)系十分密切。當(dāng)物料中的初始含碳量小于20%時,還原速率隨著含碳量的增加而明顯加快;但當(dāng)含碳量大于20%時,進(jìn)一步增加含碳量對還原速率沒有明顯的影響。
[0011]所述的真空爐窯是一種真空磚瓦窯或豎窯。傳統(tǒng)的,工業(yè)窯爐分為工業(yè)窯和工業(yè)爐,主要是指那些利用燃燒反應(yīng)把材料加熱的裝置?!案G”多應(yīng)用于硅酸鹽工業(yè)系統(tǒng),如生產(chǎn)陶瓷、玻璃、水泥等產(chǎn)品的爐子。“爐”則多用于冶金和機械系統(tǒng),主要用來冶煉和制備鋼鐵和各種
有色金屬材料。相對而言,在焙燒鈦鐵礦塊時采用窯更能提高效率,降低成本。
[0012]所述的真空磚瓦窯是一種單風(fēng)道輪窯。在磚瓦窯中,按結(jié)構(gòu)現(xiàn)有的種類有隧道窯、晾曬型輪窯、人工干燥室輪窯、直型輪窯和單風(fēng)道輪窯等種類。隧道窯是目前自動化程度最高的窯,該窯自動化程度高,設(shè)計先進(jìn)的能達(dá)到全程監(jiān)控并自動化裝出窯,降低了勞動強度并節(jié)省大量的人力資源。但是缺點是該窯投資巨大(日產(chǎn)量十萬塊標(biāo)磚的規(guī)模,總投資四百多萬元左右),且生產(chǎn)過程中維修費用過高,生產(chǎn)成本控制難度高,難以在實現(xiàn)規(guī)?;墓I(yè)化應(yīng)用。因此采用單風(fēng)道輪窯磚瓦窯才能實現(xiàn)降低生產(chǎn)成本,實現(xiàn)工業(yè)化生產(chǎn)的目的。
[0013]所述的鈦鐵礦堆垛方式采用縱橫交錯的間隔堆放方式,以提高熱量的流動性。
[0014]所述的鈦鐵礦焙燒是在60(T800°C下焙燒48小時。
[0015]焙燒完成,在真空環(huán)境下需要冷卻到400°C以下后再出爐,否則焙燒好的鈦鐵礦將在高溫下會被氧化。
[0016]本發(fā)明的鈦鐵礦冶煉新工藝,將鈦鐵礦預(yù)還原后再進(jìn)入電爐中冶煉,能夠大大減低電爐的耗電量,但又無需將鈦鐵礦研磨到IOum以下,符合現(xiàn)有的鈦鐵礦冶煉技術(shù)發(fā)展水平,是一種能夠廣泛推廣,且具備工業(yè)化應(yīng)用的新冶煉工藝。該工藝不僅節(jié)能環(huán)保,還能避免出現(xiàn)電爐中的物料塌料和翻渣現(xiàn)象,保障生產(chǎn)人員的生產(chǎn)安全。
【具體實施方式】
[0017]實施例1:用本發(fā)明的新工藝,對產(chǎn)自云南富民鈦鐵礦進(jìn)行冶煉。該原礦洗礦后,鈦鐵礦中含TiO2約45%,F(xiàn)e約35%。具體的工藝步驟如下:
(I)破碎的鈦鐵礦與焦煤進(jìn)行混合,每噸鈦鐵礦中混入焦煤0.1噸。[0018](2)將混合后的物料在高壓打磚機上壓制成塊狀。
[0019](3)壓制成塊的鈦鐵礦按燒磚堆放的方式堆垛在真空爐窯中進(jìn)行焙燒,焙燒的溫度保持800°C,焙燒48小時。
[0020](4)焙燒完成后真空下進(jìn)行冷卻至400°C以下,然后出爐。
[0021](5)出爐的塊狀鈦鐵礦破碎后投入6300kVA電爐中進(jìn)行冶煉,在冶煉溫度120(Tl800°C,可實現(xiàn)連續(xù)投料。
[0022](6)冶煉完成出料,渣鐵分離并獲得高鈦渣。
[0023]經(jīng)上述工藝冶煉后的高鈦渣,其TiO2含量在75、2%,符合國家標(biāo)準(zhǔn),但大大降低了耗能,具體體現(xiàn)如下表。
【權(quán)利要求】
1.一種鈦鐵礦的冶煉新工藝,該工藝是將破碎的鈦鐵礦進(jìn)入電爐中進(jìn)行冶煉,然后出料,渣鐵分離并獲得高鈦渣,其特征在于該鈦鐵礦在進(jìn)電爐冶煉前首先進(jìn)行預(yù)還原處理,其具體冶煉過程是: 首先,將破碎后與含碳物料混合的鈦鐵礦壓制成塊狀; 第二,將壓制成塊的鈦鐵礦在真空爐窯中進(jìn)行堆垛焙燒; 第三,焙燒完成后冷卻出爐; 最后,將出爐的鈦鐵礦投入電爐中冶煉。
2.如權(quán)利要求1所述的一種鈦鐵礦的冶煉新工藝,其特征在于按重量份,鈦鐵礦:含碳物料=1:0.08~0.12的比例進(jìn)行混料。
3.如權(quán)利要求2所述的所述的一種鈦鐵礦的冶煉新工藝,其特征在于含碳物料為焦煤。
4.如權(quán)利要求1所述的一種鈦鐵礦的冶煉新工藝,其特征在于所述的真空爐窯是一種真空磚瓦窯或豎窯。
5.如權(quán)利要求4所述的一種鈦鐵礦的冶煉新工藝,其特征在于所述的真空磚瓦窯是一種單風(fēng)道輪窯。
6.如權(quán)利要求1所述的一種鈦鐵礦的冶煉新工藝,其特征在于所述的鈦鐵礦堆垛方式采用縱橫交錯的間隔堆放 方式,以提高熱量的流動性。
7.如權(quán)利要求1所述的一種鈦鐵礦的冶煉新工藝,其特征在于所述的鈦鐵礦在真空爐窯中焙燒是在60(T80(TC下焙燒48小時。
8.如權(quán)利要求1所述的一種鈦鐵礦的冶煉新工藝,其特征在于焙燒完成,在真空環(huán)境下需要冷卻到400°C以下后再出爐。
【文檔編號】C22B4/04GK103555947SQ201310569832
【公開日】2014年2月5日 申請日期:2013年11月14日 優(yōu)先權(quán)日:2013年11月14日
【發(fā)明者】李海鷗 申請人:李海鷗
聲明:
“鈦鐵礦的冶煉新工藝的制作方法” 該技術(shù)專利(論文)所有權(quán)利歸屬于技術(shù)(論文)所有人。僅供學(xué)習(xí)研究,如用于商業(yè)用途,請聯(lián)系該技術(shù)所有人。
我是此專利(論文)的發(fā)明人(作者)