赤泥是氧化鋁工業(yè)排放的紅色粉泥狀廢棄物,屬強(qiáng)堿性有害尾渣。赤泥的產(chǎn)生量受礦石品位、生產(chǎn)方法和技術(shù)水平等因素影響。目前我國利用拜耳法工藝每生產(chǎn)1t氧化鋁會產(chǎn)生1.2~1.4t的赤泥[1]。隨著氧化鋁需求量的增大和鋁土礦品位的降低,赤泥排放量將越來越大。
國內(nèi)外實(shí)踐表明,赤泥可用作生產(chǎn)不同類型的水泥[2,3]。但由于技術(shù)和經(jīng)濟(jì)效益低的原因,國內(nèi)外氧化鋁廠通常都將赤泥輸送堆場,筑壩濕法堆存,且靠自然沉降分離對溶液返回再利用。鋁土礦中的的氟化物在氧化鋁生產(chǎn)過程中進(jìn)入赤泥,在赤泥堆場中也會滲入地下而造成水體污染[4]。裸露赤泥形成的粉塵隨風(fēng)飛揚(yáng),污染大氣,惡化生態(tài)環(huán)境[5]。因此,開展赤泥綜合利用是解決赤泥堆存造成環(huán)境污染和安全隱患的根本之策,也是我國氧化鋁工業(yè)可持續(xù)發(fā)展的必由之路[6]。
針對該問題,本課題組提出了鈣化-碳化法處理赤泥的新方法[7-8],使用該技術(shù)在處理低鋁硅比赤泥時(shí)不僅環(huán)保,而且經(jīng)濟(jì)效益良好,推廣前景廣闊。本文研究了碳化過程對赤泥回收氧化鋁的影響,尋求回收赤泥中氧化鋁的最優(yōu)碳化條件,為實(shí)現(xiàn)工業(yè)化提供依據(jù)。
1實(shí)驗(yàn)
1.1實(shí)驗(yàn)原料
實(shí)驗(yàn)所用的原料鈣化渣經(jīng)由赤泥與CaO的鈣化反應(yīng)制得。實(shí)驗(yàn)所用的赤泥來自山東某氧化鋁廠,該赤泥的主要化學(xué)成分見表1。
表1 赤泥的主要化學(xué)成分(質(zhì)量分?jǐn)?shù))
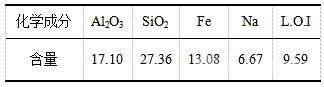
采用XRD技術(shù)對赤泥進(jìn)行了物相分析,結(jié)果如圖1所示。
圖1. 赤泥的XRD分析
由XRD分析可知,赤泥的主要物相成分為水合硅鋁酸鈉、氧化鐵和氧化硅。
對鈣化渣進(jìn)行XRD了分析,結(jié)果如圖2所示。
圖2 鈣化渣的XRD分析
從上圖中可以發(fā)現(xiàn),本實(shí)驗(yàn)的鈣化渣中主要物相為氫氧化鈣,水化石榴石以及碳酸鈣。
鈣化、溶出實(shí)驗(yàn)使用的氧化鈣、氫氧化鈉藥品均為天津市科密歐化學(xué)試劑有限公司生產(chǎn)的分析純試劑;碳化實(shí)驗(yàn)用CO2為工業(yè)用瓶裝,純度>99%。
1.2 實(shí)驗(yàn)方法
鈣化渣事先在烘干箱內(nèi)于110℃下烘干,之后經(jīng)過研磨,使其全部通過100目的標(biāo)準(zhǔn)篩。碳化過程是將鈣化渣與蒸餾水按一定液固比混合置于高壓反應(yīng)釜內(nèi),密閉、排除空氣后開始加熱、加壓,CO2壓力通過減壓閥控制。反應(yīng)結(jié)束后,碳化渣經(jīng)過分離、烘干后,取樣分析。采用電熱恒溫水浴鍋對碳化渣進(jìn)行堿溶提鋁,條件為常壓、溫度60度,堿液質(zhì)量與碳化渣質(zhì)量比:10:1,氫氧化鈉濃度:100g/L,溶鋁時(shí)間60分鐘。溶鋁反應(yīng)結(jié)束后,用蒸餾水洗滌經(jīng)過分離后的溶鋁渣兩次,烘干后取樣分析。碳化的效果通過碳化渣中氧化鋁的提取率來評判。
氧化鋁提取率計(jì)算公式如下:
式中,(A/S)泥為赤泥中的鋁硅比(Al2O3與SiO2的質(zhì)量比,下同),(A/S)渣為溶鋁后渣中的鋁硅比。
1.3 實(shí)驗(yàn)儀器
鈣化和碳化實(shí)驗(yàn)均在KTFO2-6.0型高壓釜中進(jìn)行。
固相樣品中氧化鋁和氧化硅含量采用XRF分析,鈉含量采用火焰原子吸收法分析。XRD分析使用荷蘭帕納克公司PW3040/60型X射線衍射儀(銅靶),衍射角范圍5°<2θ<90°,掃描速率0.1秒/步,步長0.0095°。
2 結(jié)果與討論
本實(shí)驗(yàn)研究的碳化過程主要是由赤泥鈣化轉(zhuǎn)型得到的水化石榴石渣與二氧化碳反應(yīng),使其碳化分解為水合硅酸鈣、碳酸鈣和含鋁化合物,產(chǎn)物中的含鋁化合物可以很容易的在堿液中溶出,而硅則以水合硅酸鈣的形式進(jìn)入渣中,從而達(dá)到鋁硅分離的目的。碳化過程的主要目的是將鈣化渣中的水化石榴石盡可能充分分解,為鋁硅分離創(chuàng)造更好的條件,有利于回收赤泥中的氧化鋁。而碳化過程對赤泥中氧化鋁提取率的影響因素主要有通氣方式,碳化溫度和碳化壓力等。
2.1通氣方式的影響
若氣體采用流動(dòng)加壓方式,如圖3(a)所示,CO2氣體通入料漿內(nèi)反應(yīng)之后隨即從釜上方的冷凝排氣口排出,調(diào)節(jié)反應(yīng)釜進(jìn)氣口流速以及出氣口流速可以控制釜內(nèi)的壓力;若采用密閉的形式如圖3(b)所示,釜內(nèi)只有一個(gè)進(jìn)氣口沒有出氣口,CO2氣體始終停留在釜內(nèi)直至被反應(yīng)吸收。
分別考察了三個(gè)不同條件下循環(huán)和密閉通氣碳化方式對氧化鋁提取率的影響。條件1為120℃、1MPa,條件2為100℃、1.0Mpa,條件3為120℃、1.2MPa。
圖4為不同條件下氧化鋁提取率的對比。
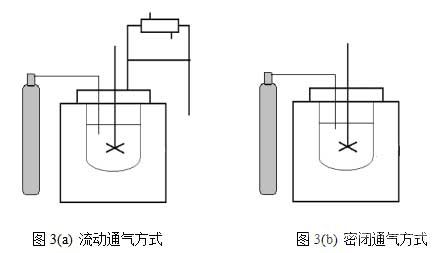
圖4 密閉與流動(dòng)條件下氧化鋁提取率的對比
由圖4可知,三種條件下流動(dòng)的通氣方式所能得到的提取率均高于密閉條件,尤其是在120℃、1.2MPa條件下差距最為明顯。這里同樣可以借助氣泡微細(xì)化的原理進(jìn)行解釋。流動(dòng)條件下的氣泡更細(xì)小、分布更加均勻,大量的細(xì)微氣泡在液體內(nèi)部創(chuàng)造出了很大的反應(yīng)面積,使得氣-液-固三相反應(yīng)更加充分,加快了反應(yīng)的傳質(zhì)傳熱及化學(xué)反應(yīng)速率的進(jìn)行,使得更多的水化石榴石被碳化分解,使氧化鋁的提取率增大。
2.2 碳化溫度的影響
溫度對反應(yīng)有著十分重要的作用,提高溫度,可以提高反應(yīng)速率,使反應(yīng)在短時(shí)間內(nèi)達(dá)到平衡。但是,升溫也有不利的一面,升溫會降低二氧化碳?xì)怏w在溶液中的溶解度和增大氣相中水蒸氣的分壓,不利于二氧化碳?xì)怏w有效濃度的保持或提高。而低溫時(shí),雖然氣體的有效濃度較高,但反應(yīng)速率較低,反應(yīng)要經(jīng)過較長的時(shí)間才能達(dá)到平衡狀態(tài),不利于反應(yīng)進(jìn)行。
圖5 碳化溫度對氧化鋁提取率的影響,(a) 1MPa,(b) 1.2MPa,(3) 1.4 MPa
圖5為碳化溫度對氧化鋁提取率的影響。由圖可以看出,在1MPa條件下,溶出率在100℃、120℃、140℃依次遞減,分別為44.5%、38.3%、34.8%;而1.2MPa下三個(gè)溫度中120℃提取率最高,為48%,100℃與140℃相近,分別為37.6%、39.6%;至于圖(c),數(shù)據(jù)顯示1.4MPa、120℃提取率最低,僅為11.2%,100℃下的提取率是32.8%,而140℃的提取率為41.3%。在碳化壓力為1.2MPa時(shí),氧化鋁的提取率隨碳化溫度提高先增加,到達(dá)120℃后出現(xiàn)下降趨勢。因?yàn)?,低溫不利于反?yīng)進(jìn)行,反應(yīng)要經(jīng)過較長的時(shí)間才能達(dá)到平衡狀態(tài),氧化鋁的提取率較低,。溫度的提高可以加快反應(yīng)速率,使化學(xué)反應(yīng)在較短的時(shí)間內(nèi)就可以達(dá)到平衡。但是,另一方面,提高溫度會降低二氧化碳?xì)怏w在溶液中的溶解度并且增大氣相中水蒸氣的分壓,從而降低了二氧化碳向溶液的溶解,不利于碳化反應(yīng)過程,從而降低了氧化鋁的提取率。
2.3 碳化壓力的影響
二氧化碳分解水化石榴石的過程是在液相中進(jìn)行的,溶解在液相與氣相中的二氧化碳按照亨利定律保持一定的平衡關(guān)系,即氣相中的二氧化碳分壓越大,在液相中溶解的二氧化碳越多。采用一定的二氧化碳分壓進(jìn)行浸出可以大大地提高反應(yīng)速度,增大反應(yīng)過程的推動(dòng)力。
圖6 碳化壓力對氧化鋁提取率的影響,(a) 100℃,(b) 120℃, (c) 140℃
由以上三圖可知,100℃條件下,提取率隨壓力的增加有所降低,壓力為1.0MPa提取率達(dá)到44.5%,壓力升至1.2MPa提取率降為37.6%,直至1.4MPa下提取率只有32.8%;而在120℃下,提取率于1.2MPa壓力下達(dá)到最高的48.0%,壓力為1MPa和1.4MPa對應(yīng)的提取率分別是38.3%,11.2%;說明在低壓的條件下,隨著壓力的增大二氧化碳?xì)怏w在溶液中的溶解度增加,二氧化碳的濃度增大,有利于二氧化碳?xì)怏w與水化石榴石的反應(yīng);當(dāng)CO2壓力過大時(shí),碳化反應(yīng)產(chǎn)生大量的碳酸鈣,其在溶鋁時(shí)與氫氧化鈉溶液發(fā)生反苛化反應(yīng),產(chǎn)物為碳酸鈉和氫氧化鈣,進(jìn)而與鋁酸根離子反應(yīng),生成水合碳鋁酸鈣,導(dǎo)致氧化鋁又進(jìn)入渣相,從而降低了氧化鋁的提取率。
3結(jié)論
1.以鈣化渣為原料的碳化和溶鋁實(shí)驗(yàn)結(jié)果表明:循環(huán)條件的溶出率相比于密閉條件有所提高。
2.溫度與壓對于溶出率的影響顯著,其中120℃、1.2MPa下溶出率可達(dá)48%,而120℃、1.4MPa的溶出率只有11.2%。
參考文獻(xiàn):
[1] 郭暉,鄒波蓉,管學(xué)茂等. 拜耳法赤泥的特性及綜合利用現(xiàn)狀[J],磚瓦,2011,09(3):50-53.
[2] M. S. Vincenzo, C. Renzo, M. Stefano. Bauxite red mud in the ceramic industry-Part2-production of clay based ceramics[J], Journal of European Ceramic Society, 2000, 20(3):245-252.
[3] M. S. Vincenzo, C. Renzo. Bauxite red mud in the ceramic industry-Part1-thermal behaviour[J], Journal of European Ceramic Society, 2000, 20(3):235-244.
[4] 陳蓓,陳素英.赤泥的綜合利用和安全堆存[J],化工技術(shù)與開發(fā),2006,35(12):32-35.
[5] 李小平.平果鋁赤泥堆場的邊坡環(huán)境問題與治理對策研究[J],有色金屬(礦山部分),2007,59(2):
29-32.
[6] 劉喜會,康志軍. 赤泥的脫堿與貯存[J],水泥,1999,08(10):4-7.
[7] 張廷安,呂國志,劉燕,等.一種基于鈣化—碳化轉(zhuǎn)型的生產(chǎn)氧化鋁方法:中國,ZL201110275013.6.[P].2012-10-31.
[8] 張廷安,呂國志,劉燕,等.一種消納拜耳法赤泥的方法:中國,201110275030.X. [P].2012-10-31.
聲明:
“碳化過程對拜耳法赤泥回收氧化鋁的影響” 該技術(shù)專利(論文)所有權(quán)利歸屬于技術(shù)(論文)所有人。僅供學(xué)習(xí)研究,如用于商業(yè)用途,請聯(lián)系該技術(shù)所有人。
我是此專利(論文)的發(fā)明人(作者)