馬斯克 2006 年公布了一個(gè)偉大的愿景:造越來(lái)越便宜的電動(dòng)車(chē),替代燃油車(chē)、加速世界轉(zhuǎn)向可持續(xù)能源。
中國(guó)正在快速接近這個(gè)目標(biāo)。這里的新能源汽車(chē)平均售價(jià)已從去年的 20 多萬(wàn)元降到 18 萬(wàn)元以?xún)?nèi),與燃油車(chē)齊平,明年還會(huì)繼續(xù)下降。造車(chē)新勢(shì)力、問(wèn)界等原本瞄準(zhǔn) 25 萬(wàn)-40 萬(wàn)元市場(chǎng)的品牌也在推出更便宜的車(chē)型。乘聯(lián)會(huì)估計(jì),2024 年中國(guó)每賣(mài) 100 輛車(chē),就會(huì)有 42 輛是新能源車(chē)。
只是,特斯拉卻正在缺席這個(gè)它參與開(kāi)啟的變革。至少在未來(lái) 18 個(gè)月里,特斯拉在中國(guó)市場(chǎng)不會(huì)有全新車(chē)型。它的 Model 3 和 Model Y 已經(jīng)沒(méi)有剛上市時(shí)的價(jià)格優(yōu)勢(shì)。特斯拉全球唯一的新車(chē)型 Cybertruck 在 2024 年的產(chǎn)量只有 12.5 萬(wàn)輛,且主要在美國(guó)交付。這款造型未來(lái)的皮卡起售價(jià)約 43 萬(wàn)元人民幣,是 2019 年首次公布時(shí)的 1.5 倍。
特斯拉早先宣布的新車(chē),低于 15 萬(wàn)元人民幣的大眾車(chē)型最早也得等到 2025 年二季度才能量產(chǎn)。到那時(shí),Model 3 已經(jīng)賣(mài)了 8 年,Model Y 已經(jīng)賣(mài)了 5 年,期間只有不改變外形的一輪改款。
使特斯拉陷入 5 年車(chē)型真空期的一大癥結(jié)是 4680 電池量產(chǎn)延期多年。
特斯拉 2020 年發(fā)布 4680 電池。在研發(fā)之初,馬斯克認(rèn)為電池制造效率太低,特斯拉可以重新發(fā)明電池制造流程,拋棄常規(guī)做法,降低 50% 成本。
4680 電池原計(jì)劃在 2021 年開(kāi)始量產(chǎn),但直到今年年中才小規(guī)模量產(chǎn)。特斯拉美國(guó)得州工廠過(guò)去 4 個(gè)月只生產(chǎn)了 1000 萬(wàn)顆 4680 電芯,只夠裝 1.2 萬(wàn)輛 Cybertruck。
《晚點(diǎn) LatePost》了解到,今年下半年,特斯拉開(kāi)始找中國(guó)電池公司代工電池極片以滿(mǎn)足產(chǎn)量要求。到明年二季度,松下會(huì)開(kāi)始給特斯拉供應(yīng) 4680 電池,但產(chǎn)能只夠裝載約 6 萬(wàn)輛車(chē)。
從 Roadster 到 Model 3,再到 Model Y,特斯拉在數(shù)代新車(chē)型上都運(yùn)用 “第一性原理” 的思考方式:即重新思考那些大多數(shù)人習(xí)以為常的慣例與陳規(guī),追根溯源分析是否合理,再?gòu)奈锢韺W(xué)原理出發(fā)尋找新的更簡(jiǎn)單和便宜的解決辦法,完成那些業(yè)內(nèi)專(zhuān)家視為不可能的目標(biāo)。4680 電池是這種做法的延續(xù)。
《馬斯克傳》中多次描述了第一性原理手到擒來(lái)的過(guò)程。在制造 SpaceX 火箭時(shí),馬斯克挑戰(zhàn)權(quán)威,提出用更便宜的不銹鋼替換碳纖維制造火箭,最終只花 NASA 登月計(jì)劃 2% 的錢(qián)就造出了能飛上太空的 Starship。
特斯拉和馬斯克執(zhí)掌的其它技術(shù)公司似乎總能憑第一性原理另辟蹊徑,證明傳統(tǒng)觀念是錯(cuò)的,一次次取得技術(shù)領(lǐng)先。
但在 4680 電池上,特斯拉的做法遇阻。這款電池決定著特斯拉下一代車(chē)的產(chǎn)能和定價(jià),而它的量產(chǎn)時(shí)間和性能都沒(méi)有達(dá)到最初發(fā)布時(shí)的目標(biāo)。這是近年被不少公司奉為至寶的第一性原理的另一面:當(dāng)遇上復(fù)雜創(chuàng)新,從原理出發(fā)推導(dǎo)重來(lái)常常只是一趟艱難旅程的起點(diǎn)。
重新發(fā)明電池和電池工廠
馬斯克提出過(guò) “白癡指數(shù)”:用零件的價(jià)格除以這個(gè)零件所需原材料的成本。這個(gè)數(shù)字越大,說(shuō)明這個(gè)零部件 “越白癡”,要么是中間環(huán)節(jié)太多,要么是制造效率太低。
每當(dāng)遇到一個(gè)白癡指數(shù)過(guò)高的部件,特斯拉就會(huì)重新思考流程、革新制造方式以降低成本,使該指數(shù)盡量回歸 “1”。馬斯克追求讓汽車(chē)的制造成本無(wú)限接近汽車(chē)所用的鋼鐵、鋁、硅、鋰等材料的成本之和。
2007 年,馬斯克查詢(xún)倫敦金屬交易所的電池材料價(jià)格后,算出電池的 “白癡指數(shù)” 是 7:當(dāng)時(shí)每瓦時(shí)電池的鋰、鈷、鎳等材料的成本只有 82 美元,但鋰電池售價(jià)卻超過(guò) 600 美元,這一數(shù)字已是索尼、松下等電池公司努力 20 年的結(jié)果。
特斯拉在 2014 年與松下合資建立電池超級(jí)工廠,期望以此降低電池成本。但到 2020 年,鋰電池的 “白癡指數(shù)” 仍有 2,當(dāng)時(shí)整車(chē)的實(shí)際白癡指數(shù)已小于 1.5。特斯拉仍得把汽車(chē)賣(mài)到 4 萬(wàn)美元(約 30 萬(wàn)元人民幣,也就是 Model 3 的售價(jià))才能保持毛利,馬斯克認(rèn)為這還不夠便宜。
同在 2020 年,特斯拉宣布將研發(fā)制造售價(jià)約 2.5 萬(wàn)美元(按當(dāng)時(shí)匯率計(jì)算約為 15 萬(wàn)元人民幣)的低價(jià)電動(dòng)車(chē),以進(jìn)入更主流汽車(chē)市場(chǎng),與豐田卡羅拉等最暢銷(xiāo)車(chē)型直接競(jìng)爭(zhēng)。
支撐這一目標(biāo)的是一個(gè)完整的電池降本計(jì)劃。自 2018 年起,特斯拉成立代號(hào) “跑路者”(Roadrunner)的項(xiàng)目組,開(kāi)始籌劃自研和自產(chǎn)電池。
第一性原理思考的本意是:不停質(zhì)疑你能質(zhì)疑的所有事,直到只剩下基礎(chǔ)的事實(shí)與原理。特斯拉工作法中的第一條就是:“質(zhì)疑每項(xiàng)要求”。
以這個(gè)視角看電池制造,特斯拉圍繞降本目標(biāo)更改了圓柱電池的尺寸,簡(jiǎn)化了延續(xù)幾十年的濕法生產(chǎn)再烘干的繁復(fù)環(huán)節(jié),設(shè)計(jì)了新的電池與制造流程。
特斯拉選擇大圓柱結(jié)構(gòu):把圓柱電池的尺寸從直徑 21 毫米、長(zhǎng) 70 毫米提升至直徑 46 毫米、長(zhǎng) 80 毫米,這即是 “4680” 電池名稱(chēng)的由來(lái)。更大的圓柱結(jié)構(gòu),能提升單個(gè)電池中的能量物質(zhì)占比,進(jìn)而提升電池能量密度。
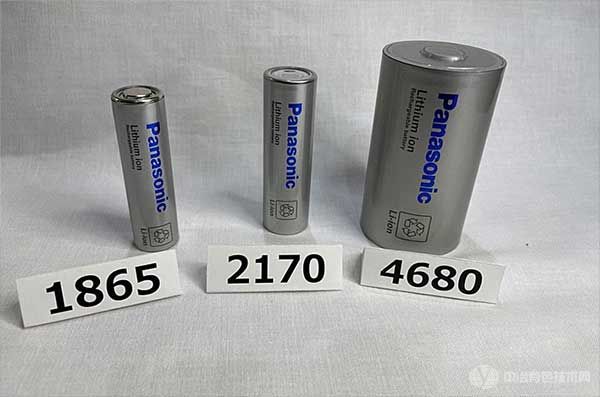
特斯拉使用的三種不同尺寸的圓柱電池。圖源:松下官方。
這一設(shè)計(jì)兼顧了制造效率與成本。目前主流的動(dòng)力電池分為圓柱和方形電池。圓柱形物體在流水線中的運(yùn)轉(zhuǎn)速度高于方形物體。方形電池龍頭寧德時(shí)代每分鐘能生產(chǎn) 25 個(gè)電芯,而圓柱電池龍頭松下每分鐘能生產(chǎn) 300 個(gè) 2170 電芯。圓柱電池的弊端是,在封裝為電池包時(shí),圓柱與圓柱間會(huì)有縫隙,空間利用率低于方形電池。
圓柱電池在排列時(shí)會(huì)留下縫隙。
大圓柱能大幅減少縫隙。一位電池公司研發(fā)負(fù)責(zé)人表示,車(chē)用圓柱電池直徑控制在 45- 50 毫米時(shí)能最好地兼顧電池容量和空間利用率,如果尺寸再大,加工難度會(huì)提高,對(duì)空間利用率的提升也會(huì)變少。
“尺寸變大” 看著只是一個(gè)小改動(dòng),實(shí)際會(huì)帶來(lái)一系列相互矛盾的改進(jìn)。只把電池做大,極耳,即連接電池內(nèi)外部電路的導(dǎo)電部分就要承擔(dān)更多電流,更容易熱失控,增大安全隱患。
圖中突出的綠色和灰色部分為正負(fù)極耳。來(lái)源:逸飛激光招股書(shū)。
“既然極耳朵不聽(tīng)話,那就扔掉它?!?馬斯克說(shuō)。特斯拉隨即去掉了電池極耳,改為讓整個(gè)電池底部和外殼充當(dāng)極耳,這即是 “全極耳”(也稱(chēng) “無(wú)極耳”)工藝,它能加快電池充電速度,還讓電池更容易散熱——電池外殼體積比原本的小片突起的極耳更大,更容易散熱。
電池公司在過(guò)去 30 年一直使用濕法工藝。它們將電池材料與有毒的粘合劑、液態(tài)溶劑混合,然后涂在薄薄的箔片上。加工完的極片要在長(zhǎng)達(dá) 100 米、溫度達(dá) 90 度的烘箱中烘烤 12 個(gè)小時(shí),在這個(gè)過(guò)程中充分蒸發(fā)有毒的溶劑和水分——整個(gè)工序極大增加制造成本。
特斯拉認(rèn)為濕法工藝很低效:既然極片要做成 “干” 的,為什么要先把極片弄濕、再烘干?這就是馬斯克覺(jué)得電池制造的白癡部分。濕法涂布的設(shè)備、人工、廠房成本占整個(gè)電池制造的 22.76%。
2019 年 2 月,特斯拉花 2.19 億美元買(mǎi)下超級(jí)電容(用于攝像機(jī)閃光燈等領(lǐng)域的電能儲(chǔ)存設(shè)備)公司 Maxwell,將超級(jí)電容器的干法電極工藝改用到鋰電池中,直接把極片做成干的。
干法電極不使用液態(tài)粘合劑,因此不需要烘烤,理論上制造起來(lái)更便宜、更快,對(duì)環(huán)境的破壞也更小。馬斯克說(shuō),僅靠這個(gè)工藝,特斯拉就能將單位產(chǎn)能的設(shè)備支出減少三分之一,將電極生產(chǎn)車(chē)間的占地面積和能源損耗減少 90%。
目前一條方形電池產(chǎn)線的設(shè)備支出約為 1.7 億元人民幣,而 4680 電池產(chǎn)線的設(shè)備支出僅需 5000 萬(wàn)-6000 萬(wàn)元。
特斯拉還希望加速電池流水線,來(lái)提升生產(chǎn)效率。馬斯克羨慕啤酒等飲料制造業(yè)和造紙業(yè)的連貫與超高效率:造啤酒時(shí),生產(chǎn)線沒(méi)有任何斷點(diǎn),啤酒瓶封上蓋后才會(huì)離開(kāi)生產(chǎn)線,但電池的部分部件造完后,通常都要暫時(shí)離開(kāi)生產(chǎn)線,靠小車(chē)運(yùn)到下一個(gè)車(chē)間,再回到流水線上?,F(xiàn)在最快的電池生產(chǎn)線運(yùn)轉(zhuǎn)速度為 6 公里 / 小時(shí),而最快的啤酒生產(chǎn)線可達(dá) 30 公里 / 小時(shí)。
特斯拉為此大幅合并了電池制造工序,開(kāi)發(fā)集合多個(gè)工藝的設(shè)備。如 2021 年,特斯拉在柏林工廠啟用了切割、卷繞和焊接的三合一一體機(jī),這些任務(wù)本來(lái)需要 3 臺(tái)不同的設(shè)備才能完成。
按馬斯克在 2020 年的說(shuō)法,整個(gè) 4680 電池方案能減少約 20% 的電池的制造成本,35% 的設(shè)備投資成本和 70% 的工廠占地面積。
當(dāng)時(shí)的特斯拉將 4680 電池視為大規(guī)模擴(kuò)張的基礎(chǔ):用投資更少的電池工廠生產(chǎn)儲(chǔ)能和汽車(chē)電池,再用更便宜的電池制造售價(jià) 2.5 萬(wàn)美元的廉價(jià)車(chē)型,刺激銷(xiāo)量、賺取更多利潤(rùn),再投入到研發(fā)和新一輪產(chǎn)能擴(kuò)張,形成增長(zhǎng)飛輪,助力特斯拉在 2030 年實(shí)現(xiàn)一年賣(mài) 2000 萬(wàn)輛車(chē)的宏大目標(biāo)。
完美的設(shè)計(jì),艱難的制造
做大電池,去掉弄濕電機(jī)再烘干的 “白癡部分”。這些顯而易見(jiàn)的改進(jìn)在過(guò)去數(shù)十年的電池工業(yè)中從未被實(shí)踐,因?yàn)槔щy重重。
第一個(gè)難題是流程改造。
汽車(chē)制造流程相對(duì)短,且對(duì)精度和環(huán)境的控制要求較低,汽車(chē)制造的主要任務(wù)是成品組裝,改進(jìn)一個(gè)組裝工序很少影響前后工序。電池制造則是將材料變成成品,流程相關(guān)性更強(qiáng),前一個(gè)工序的成品就是后一個(gè)工序的原料。改進(jìn)一個(gè)工序,意味著也要修改前后工序。
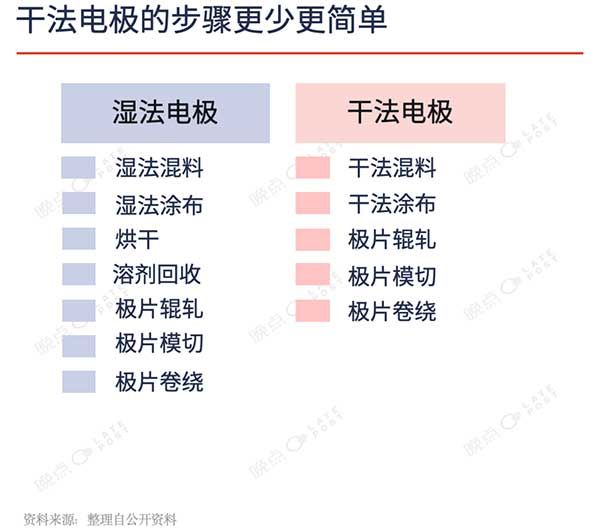
特斯拉為了使用干法電極技術(shù),去掉烘干等步驟,就需要把烘干前的所有環(huán)節(jié)都變成 “干” 的。這占整個(gè)電池制造流程的 50% ,且對(duì)環(huán)境、精度的控制遠(yuǎn)高于其余工序。
濕法電極的核心是涂布。它的任務(wù)像抹奶油,把帶有粘結(jié)劑的糊狀電池正負(fù)極材料均勻涂抹在金屬箔片上,涂抹厚度一般只有 30 微米。寧德時(shí)代等電池公司致力于提升涂布速度,現(xiàn)已能做到每分鐘涂 100 米。涂布速度越快、質(zhì)量控制越難。細(xì)微提升背后,靠的是數(shù)十億次嘗試中總結(jié)的經(jīng)驗(yàn)。
干法電極同樣要在金屬箔片上附著正負(fù)極材料,但正負(fù)極材料為干粉狀,附著力弱,它不像抹奶油,而更像撒沙子,且同樣追求均勻度和速度。
為把沙子撒得均勻、粘得牢固,特斯拉研發(fā)了新的粘結(jié)劑。
2020 年,特斯拉申請(qǐng)了干法電極粘結(jié)劑專(zhuān)利,它改進(jìn)了鋰電池原本采用的 PVDF 粘結(jié)劑。從微觀層面看,這種新粘結(jié)劑被滾壓后會(huì)纖維化,就像一張網(wǎng)。這讓原本在平面上撒沙子變成 “就像在棉花糖上撒沙子”,一位干法電極工藝專(zhuān)家說(shuō)。
但當(dāng)時(shí)的特斯拉并不清楚要在正負(fù)極材料里混合多少粘結(jié)劑:粘結(jié)劑比例高了,電池中帶能量的物質(zhì)就會(huì)變少,能量密度會(huì)變低,且粘結(jié)劑會(huì)阻礙鋰離子在電池中的流動(dòng),這會(huì)縮短電池循環(huán)壽命;但粘結(jié)劑比例太低,材料的附著力又不夠。
衡量粘結(jié)劑效果的一個(gè)直觀標(biāo)準(zhǔn)是電池首效(第一次充放電時(shí)電池的電量占設(shè)計(jì)容量的比例)。一位拆解過(guò) 4680 電池的工程師稱(chēng),特斯拉在今年年中的樣品能將首效做到 88%,而其他參與該項(xiàng)目的電池公司只能做到 85%,但還未達(dá)到量產(chǎn)電池的水準(zhǔn)。目前主流的動(dòng)力電池首效超過(guò) 92%。
“以這個(gè)首效推算,特斯拉 4680 電池的循環(huán)次數(shù)可超過(guò) 1000 次,但目前主流的電池的循環(huán)次數(shù)超過(guò) 2500 次。” 他說(shuō)。
材料研發(fā)還只解決了約 20% 的量產(chǎn)難題 ,接下來(lái)還有設(shè)備研發(fā)。
干法電極設(shè)備需要用合適的力度將材料中的粘結(jié)劑滾壓成合適的纖維化狀態(tài)。在實(shí)驗(yàn)室環(huán)境中,這件事很簡(jiǎn)單。但大規(guī)模生產(chǎn)要求設(shè)備能連續(xù)、精準(zhǔn)地處理整個(gè)任務(wù)。
輥壓要多次進(jìn)行,如果只壓一次,就沒(méi)有足夠的操作空間來(lái)調(diào)整設(shè)備參數(shù)。特斯拉公開(kāi)的專(zhuān)利中,采用了三個(gè)滾輪,分兩次執(zhí)行輥壓動(dòng)作。但一位接近設(shè)備供應(yīng)商的人士稱(chēng),特斯拉后來(lái)將輥壓設(shè)備的滾輪數(shù)量增加到了 7 個(gè)。
目前行業(yè)使用的干法電極設(shè)備。
越來(lái)越多的滾輪確實(shí)提升了精度上限,但又增加了調(diào)試難度,每調(diào)整一次前面的滾輪,后續(xù)所有滾輪的參數(shù)都會(huì)變化。
在制造領(lǐng)域時(shí)常靈光乍現(xiàn),敢于嘗試的特斯拉,也不得不陷入這樣的低效怪圈。調(diào)試設(shè)備和工藝沒(méi)有捷徑,它需要一次次嘗試。且往往牽一發(fā)動(dòng)全身,改一處得調(diào)整多個(gè)環(huán)節(jié)。去掉弄濕正負(fù)極材料再烘干的 “多余環(huán)節(jié)”,比馬斯克最初想象得難得多。
特斯拉的做法是自己設(shè)計(jì)設(shè)備,再找鋰電設(shè)備公司做代工生產(chǎn),幫助克服一些設(shè)備問(wèn)題。
一位曾接觸過(guò)特斯拉的設(shè)備供應(yīng)商人士稱(chēng),特斯拉會(huì)給到設(shè)備核心圖紙,并限制供應(yīng)商修改設(shè)計(jì)?!白罱K的結(jié)果是,設(shè)備工程師不懂工藝,特斯拉的人不懂設(shè)備,設(shè)備供應(yīng)商花了很長(zhǎng)時(shí)間才造出能用的設(shè)備,但依然不符合特斯拉的要求?!?他說(shuō)。
2021 年,特斯拉找了多家電池設(shè)備供應(yīng)商制造設(shè)備,其中部分設(shè)備方案現(xiàn)已被舍棄?!锻睃c(diǎn) LatePost》了解到,一家龍頭鋰電設(shè)備供應(yīng)商曾向特斯拉提供了整條 4680 產(chǎn)線設(shè)備,并派出一個(gè)近 50 人的工程團(tuán)隊(duì)去得州協(xié)助特斯拉優(yōu)化產(chǎn)線,該團(tuán)隊(duì)已在 2022 年底撤走。
生產(chǎn)設(shè)備的另一個(gè)難點(diǎn)是焊接機(jī)。
原本的電池極耳只有一小片,而 4680 電池采用全極耳設(shè)計(jì),需要焊接的極耳面積成倍增加。焊接面積越大,就越容易出錯(cuò)。焊接機(jī)輸出的能量過(guò)大會(huì)焊穿極耳,能量不夠焊接就不牢固,兩種情況都會(huì)讓電池報(bào)廢。
“特斯拉到今年也沒(méi)有明確定義焊接效果要做到什么樣。特斯拉從源頭去革新,但到落地的細(xì)枝末節(jié)上他們也把不準(zhǔn),于是就花錢(qián)找人幫他圓夢(mèng)。” 一位設(shè)備供應(yīng)商人士稱(chēng),特斯拉并未給出更好的極耳焊接控制方案。此外,特斯拉還在激光密封等環(huán)節(jié)遇到了良率挑戰(zhàn)。
到去年年末,特斯拉的 4680 電池生產(chǎn)良率只有 92%。依照電池行業(yè)測(cè)算,4680 電池的良率要超過(guò) 95%,才能壓低成本,實(shí)現(xiàn)商用。
特斯拉生產(chǎn)線的效率也遠(yuǎn)未達(dá)到行業(yè)的預(yù)期。一位設(shè)備廠商人士稱(chēng),今年初,特斯拉 4680 電池的生產(chǎn)效率約為 85 個(gè) / 分鐘,此前行業(yè)認(rèn)為 4680 電池的效率上限是 350 個(gè) / 分鐘。
當(dāng)特斯拉的生產(chǎn)線以更快的速度運(yùn)行時(shí),制造過(guò)程中的品控難題還會(huì)繼續(xù)出現(xiàn)。
“即使只漏掉 0.001% 的灰塵和碎片,這些東西也會(huì)導(dǎo)致電池短路,實(shí)驗(yàn)室環(huán)境不會(huì)放大細(xì)微的可能性,但工廠會(huì)。你會(huì)一直發(fā)現(xiàn)新的失敗方式?!?特斯拉電池項(xiàng)目負(fù)責(zé)人德魯·巴格利諾在今年 3 月的投資者日上說(shuō)。
目前,特斯拉的 4680 電池制造方案還未定型?!皢?wèn)題不止在生產(chǎn),設(shè)計(jì)也在修改,時(shí)常是一個(gè)流程還沒(méi)順完,就要開(kāi)始做下一個(gè)版本?!?一位特斯拉工程師告訴《晚點(diǎn) LatePost》。
只有特斯拉才敢這樣造電池
據(jù)行業(yè)人士測(cè)算,如果不執(zhí)著于干法電極,4680 電池也能將 Model Y 的成本削減約 8%,也就是將電池成本削減 20%。雖然這還不到馬斯克目標(biāo)的一半,但放在動(dòng)力電池行業(yè)已是了不起的成就,松下、寧德時(shí)代需要至少三年才能達(dá)成類(lèi)似的降本成果。
特斯拉卻堅(jiān)持開(kāi)發(fā)干法電極工藝,甚至不惜拖延 Cbyertruck 和下一代車(chē)的交付節(jié)奏。在馬斯克的設(shè)想里,4680 電池并不只服務(wù)年銷(xiāo) 200 萬(wàn)輛特斯拉的當(dāng)下,而是要支持年銷(xiāo) 2000 萬(wàn)輛的未來(lái)。
只有更便宜的電池才能支持特斯拉造出 2.5 萬(wàn)美元的廉價(jià)車(chē)型,達(dá)到這個(gè)目標(biāo)。今年 3 月,特斯拉已完成車(chē)型研發(fā),并突破了更大規(guī)模的一體壓鑄技術(shù)。4680 電池成了阻礙計(jì)劃的最后一塊絆腳石。
汽車(chē)行業(yè),只有特斯拉會(huì)這樣不惜代價(jià)超前投入技術(shù),并將自己的商業(yè)擴(kuò)張與技術(shù)突破綁定在一起。收益與風(fēng)險(xiǎn)都被放大。
特斯拉此前的成功和當(dāng)下的遭遇,都出自第一性原理衍生的方法論:拋棄行業(yè)成規(guī)、質(zhì)疑原有要求,從最本質(zhì)的物理學(xué)出發(fā)重新想一件事該怎么做。
這一方法論能行得通的情境往往是:特斯拉要挑戰(zhàn)和顛覆的是某一技術(shù)階段產(chǎn)生的老做法或習(xí)慣,而現(xiàn)在已經(jīng)有新技術(shù)可以繞開(kāi)曾經(jīng)的制約。馬斯克敏銳地看出過(guò)去的限制已不復(fù)存在,捅破了那層資深專(zhuān)家腦中隱形的 “不可能”,直抵解決之道。
這需要技術(shù)直覺(jué)和判斷。但馬斯克或任何個(gè)人都難以客觀全面地評(píng)估一個(gè)時(shí)期的整體技術(shù)與工程水平。
有些情況下,馬斯克的想法剛好能找到技術(shù)與工程支持:當(dāng)他從玩具制造上想到一體壓鑄時(shí),地球上剛好存在一家能制造出 6000 噸壓鑄機(jī)的公司——力勁。
SpaceX 使用的 33 臺(tái)發(fā)動(dòng)機(jī)并聯(lián)推進(jìn)方案,也是蘇聯(lián)科學(xué)家在 1970 年代嘗試過(guò)卻失敗的設(shè)想?;鸺l(fā)動(dòng)機(jī)在推流時(shí)會(huì)互相影響,需要實(shí)時(shí)調(diào)整發(fā)動(dòng)機(jī)設(shè)置。當(dāng)時(shí)的計(jì)算機(jī)無(wú)法同時(shí)控制這么多發(fā)動(dòng)機(jī)。而到 SpaceX 落地這一設(shè)想的 2023 年,計(jì)算機(jī)算力和算法已能完成復(fù)雜任務(wù)——主流 AI 芯片的算力是 50 年前的 10 億倍。
在以上這些例子中,馬斯克回到原點(diǎn),重新思考了那些多年來(lái)被不假思索接受的習(xí)慣。在歷史悠久的汽車(chē)業(yè)和航天業(yè),大型廠商日復(fù)一日沿既定生產(chǎn)流程追求生產(chǎn)效率的極致,難有跳出來(lái)思考的意識(shí)或余裕。
第一性原理的局限則是它不可能超越時(shí)代限制。當(dāng)特斯拉的目標(biāo)無(wú)法被當(dāng)下的技術(shù)實(shí)現(xiàn),它也得付出巨大的時(shí)間與金錢(qián)投入,才能緩慢前進(jìn)一點(diǎn)點(diǎn)。
2017 年量產(chǎn) Model 3 時(shí),特斯拉曾栽過(guò)跟頭:馬斯克當(dāng)時(shí)認(rèn)為可以用機(jī)械臂完全取代人工,這是制造業(yè)的必然。但他高估了整個(gè)自動(dòng)化技術(shù)的水平,機(jī)械臂連簡(jiǎn)單的梳理電線都做不好。特斯拉隨即陷入產(chǎn)能地獄,馬斯克重新把工人召回工廠才走出危機(jī)。
電池制造也是這樣一個(gè)領(lǐng)域:它涉及多學(xué)科復(fù)雜任務(wù),工序之間環(huán)環(huán)相扣,牽一發(fā)動(dòng)全身?!坝脻竦恼?fù)極材料涂布、再烘干”,這是馬斯克最初認(rèn)為多此一舉的環(huán)節(jié)。但刪除這個(gè)環(huán)節(jié),就需要把整個(gè)從混料、涂布、模切到烘干的工藝都推倒重來(lái)。
即使特斯拉能在實(shí)驗(yàn)室里完成上述流程,接下來(lái)它還得解決大規(guī)模量產(chǎn)和商業(yè)化兩個(gè)相輔相成的難題。100 萬(wàn)輛電動(dòng)車(chē)對(duì)應(yīng)十多億顆電芯,這需要在同一套設(shè)備上重復(fù)數(shù)十億次生產(chǎn)工藝,并達(dá)到一定的良率基準(zhǔn)線,且控制好成本。
多位行業(yè)人士預(yù)測(cè),特斯拉會(huì)在 2025 年大規(guī)模量產(chǎn) 4680 電池,但最終量產(chǎn)的版本性能將比 2020 年發(fā)布時(shí)的版本大幅縮水。特斯拉目前生產(chǎn)的 4680 電池能量密度只有 265Wh/kg ,比行業(yè)預(yù)測(cè)的 330Wh/kg 低近 20%。搭載這款電池的 Cybertruck 的最高續(xù)航只有 547 公里,遠(yuǎn)低于此前 800 公里的目標(biāo)。
從 4680 電池發(fā)布至今,特斯拉用 3 年時(shí)間只實(shí)現(xiàn)了最初目標(biāo)的 1/3,量產(chǎn)了工藝更簡(jiǎn)單的干法石墨負(fù)極,但接下來(lái)還有更難的干法硅負(fù)極和正極。
站在殘酷的商業(yè)競(jìng)爭(zhēng)角度:慢,有時(shí)不可接受。特斯拉的產(chǎn)品節(jié)奏被打亂。在最應(yīng)該乘勝追擊的時(shí)刻,特斯拉的新車(chē)斷檔幾年。
而站在技術(shù)進(jìn)化的角度,特斯拉給整個(gè)行業(yè)探了路:4680 電池統(tǒng)一了大圓柱動(dòng)力電池的尺寸標(biāo)準(zhǔn);目前,寧德時(shí)代等電池巨頭也開(kāi)始探索干法電極工藝,將這一工藝?yán)砟钔卣怪岭姵馗裟さ炔考?680 電池可能正在帶動(dòng)動(dòng)力電池制造的一次技術(shù)革命。