2023年,美歐航空工業(yè)強國大力推動航空制造技術(shù)創(chuàng)新發(fā)展。復合材料成形、增材制造、金屬加工、裝配與維修等領域的數(shù)字化、智能化轉(zhuǎn)型進程加速,高精度、高效率特征愈發(fā)突出,先進技術(shù)不斷涌現(xiàn),有力保障了航空產(chǎn)品高質(zhì)量研制生產(chǎn)和保障。
我們以技術(shù)重大性、前沿突破性、推廣應用性、綠色環(huán)保性等為參考依據(jù),經(jīng)系統(tǒng)梳理和專家評議,遴選出航空制造技術(shù)領域十大進展(排序不分先后),供廣大從業(yè)者參考。
英國采用超高速沉積技術(shù)實現(xiàn)17米長機翼蒙皮預制件成形
11月,英國國家復合材料中心利用其開發(fā)的全球首個復合材料超高速自動沉積系統(tǒng),制造并交付了17米長的全尺寸機翼原型。該系統(tǒng)包含兩座高7米、寬13米的龍門架,龍門架可沿26米的軌道延伸,能夠自動定位末端執(zhí)行器、切割干纖維材料并沉積到復雜雙曲率模具上,整個過程無需人工干預。在開發(fā)測試中,該系統(tǒng)能夠提供超過350千克/小時的干纖維沉積率,遠超當前大型航空結(jié)構(gòu)纖維自動鋪放量50千克/小時的水平。機翼原型自動化成形涉及大約170層單獨的干纖維鋪層,在生產(chǎn)過程中最大沉積速率接近0.8米/秒,完成一層17米的鋪層只需大約30秒。此外,團隊還實現(xiàn)了世界上首次大規(guī)模、高度復雜的一體化結(jié)構(gòu)樹脂灌注。
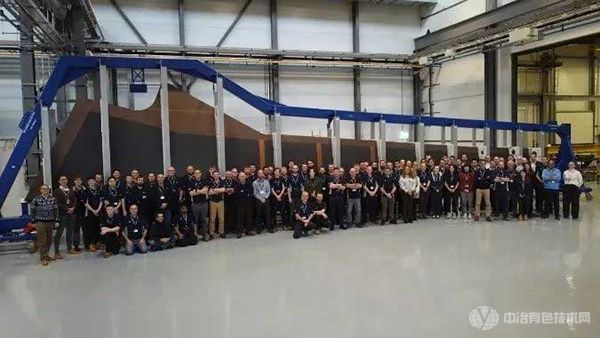
【述析】
面對未來廣闊的民機市場,“大(部件)且快(成形)”是下一代大飛機的發(fā)展焦點和競爭高地,高速、低成本航空復合材料制造技術(shù)已成為核心關切。該機翼原型為空客“明日之翼”項目的研究成果,“明日之翼”項目于2016年啟動,旨在通過改進制造工藝、開發(fā)自動化程度更高的新裝配方法等完成機翼集成,從而提高未來單通道飛機產(chǎn)量。英國國家復合材料中心牽頭的系列研究成果實現(xiàn)了纖維沉積速率提升6倍,并探索了高度復雜的一體化結(jié)構(gòu)樹脂灌注,在復合材料主結(jié)構(gòu)高速成形和非熱壓罐制造上取得了重大突破,有望大幅釋放復合材料結(jié)構(gòu)制造產(chǎn)能,持續(xù)提升未來航空產(chǎn)品生產(chǎn)效率。
歐盟“多功能機身驗證件”項目交付熱塑性上、下機身段
2月,在空客公司牽頭的“多功能機身驗證件”項目下,吉凱恩??藞F隊完成了熱塑性下機身段的制造,該部件尺寸8米×4米,由400多個熱塑性纖維增強零件、數(shù)千個焊點和數(shù)百米的連續(xù)焊縫組成,是世界上最大的熱塑性復合材料部件之一;7月,德國航空航天中心團隊完成了熱塑性上機身段的制造,該部件采用激光原位加熱輔助絲束鋪放、機器人連續(xù)超聲焊和協(xié)作機器人電阻焊技術(shù),這些技術(shù)將使完整的機身段總重減少1噸(10%),月產(chǎn)量達到至少60架(最多100架),并且機身經(jīng)常性總成本減少100萬歐元(20%)。
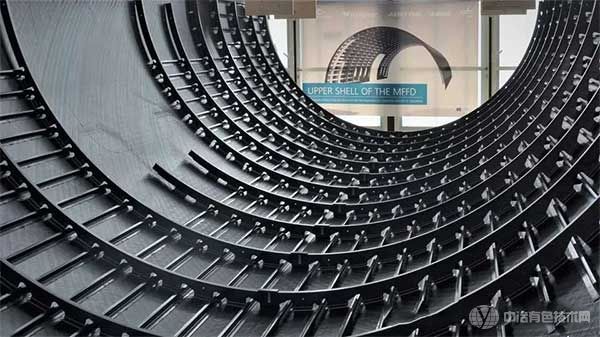
【述析】
歐盟通過“框架計劃”和“潔凈天空”系列計劃等,為高效、低碳的航空制造技術(shù)提供了持久、穩(wěn)定的預研支持,是下一代大飛機研發(fā)的重要基礎。作為“潔凈天空2”下的研究項目,“多功能機身驗證件”的成果是歐盟實施熱塑性復合材料航空主結(jié)構(gòu)發(fā)展路線圖的關鍵里程碑。項目將高強輕質(zhì)、可回收熱塑性復合材料作為實現(xiàn)未來可持續(xù)航空的抓手,成功制造出了世界上最大的熱塑性部件單件,在線檢測、機器人焊接等先進技術(shù)的成功應用使得龐大的機身結(jié)構(gòu)高效成形并充分減重,可以說是熱塑性復合材料進軍航空大型結(jié)構(gòu)件應用的標桿實踐。
東麗公司開發(fā)可用于熱固性復合材料的高速熱焊接技術(shù)
2月,日本東麗工業(yè)公司開發(fā)了一種可以高速熱焊接碳纖維增強熱固性復合材料部件的技術(shù),該技術(shù)通過在部件表面形成熱焊接層,通過瞬間加熱表面以實現(xiàn)部件粘合,無需粘合劑粘合或螺栓緊固。東麗公司使用熱焊接的熱固性復合材料部件組裝了一個模擬飛機基本結(jié)構(gòu)的演示驗證機,驗證了其力學性能和連接強度與目前機型的共固化復合材料結(jié)構(gòu)相當。該技術(shù)預期在2030年后實現(xiàn)機身商業(yè)化應用,有望實現(xiàn)與鋁合金機身相當或超過鋁合金機身的生產(chǎn)速度,同時還可減少復合材料機身壽命周期內(nèi)的碳排放并減輕重量。
【述析】復合材料結(jié)構(gòu)的焊接連接是減少緊固重量、提高成形速度和可靠性的有效手段,這一連接手段過去只能在熱塑性復材結(jié)構(gòu)上實現(xiàn)。東麗公司開發(fā)的高速熱焊接技術(shù)另辟蹊徑,通過在熱固性復合材料的表面形成熱焊接層并加熱實現(xiàn)了結(jié)構(gòu)粘合,且性能和強度符合要求,同時避免了整體更換和鑒定熱塑性材料的復雜環(huán)節(jié),是一項具有快速高效、綠色環(huán)保和推廣應用潛力的突破性創(chuàng)新。
諾?格公司開發(fā)應用于高超聲速武器的機器人增材制造系統(tǒng)
1月,諾·格公司使用增材制造技術(shù)開發(fā)了“超聲速吸氣式武器概念”項目的高超聲速燃燒沖壓發(fā)動機,并與電沖擊公司一同完善可擴展碳-碳復合材料機器人增材制造系統(tǒng),以實現(xiàn)航空級集成復合材料結(jié)構(gòu)的無模具快速制造。利用基于增材制造的快速成形工藝,該系統(tǒng)能夠制造在暴露于極端溫度時不會腐蝕、熔化或改變形狀的碳-碳耐高溫結(jié)構(gòu),成本和進度縮減可高達50%。項目團隊制造了一個以圓形橫截面開始、S形彎曲并以矩形橫截面結(jié)束的零件,此類復雜幾何形狀的零件過去只能手工制作,且可能需要長達一年的時間,利用該增材制造系統(tǒng)則可以在幾周內(nèi)完成。

【述析】
耐高溫復雜結(jié)構(gòu)的快速試制與生產(chǎn)是支撐高超聲速武器快速發(fā)展的重要環(huán)節(jié)。該成果體現(xiàn)了諾·格公司在高超聲速武器耐高溫碳-碳結(jié)構(gòu)制造中對復合材料增材制造技術(shù)應用的領先探索,電沖擊公司給出了基于六軸機器人的可擴展連續(xù)纖維增材制造解決方案,提升了成形過程的靈活性,例如可定制每層內(nèi)的纖維取向以提供最佳的強度和剛度分布。從初步成效看,增材制造技術(shù)在快速實現(xiàn)設計意圖、按需整體生成復雜零件方面具有顯著優(yōu)勢,更重要的是能夠打破設計壁壘,為高超聲速武器結(jié)構(gòu)的“天馬行空”創(chuàng)新研制提供了條件保障。
吉凱恩公司推出全球最大激光定向能量沉積增材制造單元
6月,吉凱恩航宇公司推出目前世界上最大的Cell 3激光定向能量沉積增材制造單元,是突破大尺寸鈦合金飛機結(jié)構(gòu)增材制造界限的新一代設備。該制造單元配備20千瓦激光器,具有多達10個運動軸,最大構(gòu)建尺寸為5.6米×2.5米,采用雙面或旋轉(zhuǎn)沉積方式,能夠使用線材激光金屬沉積工藝制造5米長的鈦合金部件。該制造單元不僅可以滿足對安全把控極其嚴苛的航空結(jié)構(gòu)所需尺寸,而且可以顯著加快生產(chǎn)速度,縮短交付時間。
【述析】
當前,金屬增材制造的沉積效率和尺寸限制制約了其規(guī)?;瘧茫咚俾?、大幅面增材制造成為重點攻關方向。與其他金屬沉積工藝相比,線材激光金屬沉積工藝具有可調(diào)節(jié)激光能量和金屬絲進給速率等優(yōu)點,進而可以有效控制沉積速率和產(chǎn)品性能。2022年,吉凱恩公司利用Cell 2單元研制出了尺寸達2.5米級的鈦金屬構(gòu)件,一度成為行業(yè)里程碑。在此基礎上,吉凱恩公司持續(xù)發(fā)力,新的Cell 3單元將最大鈦合金構(gòu)件尺寸突破至5米級,且成形方式更靈活、效率更高。隨著對工藝改進、建模與仿真、無損評估方法、現(xiàn)場監(jiān)測等的持續(xù)研究,該技術(shù)有望在更多種類、更大尺寸的高價值難加工飛機和發(fā)動機金屬結(jié)構(gòu)上發(fā)揮應用優(yōu)勢。
美英開發(fā)下一代可消耗無人機集群批量增材制造解決方案
6月,美國風暴實驗室公司與英國綠色推進公司宣布將合作開發(fā)全增材制造的無人機機身和發(fā)動機批量生產(chǎn)解決方案。風暴實驗室公司擁有獨特的互聯(lián)增材制造和可互換機身組件技術(shù),支持無人機搭載通用平臺和基于人工智能的飛行計算機執(zhí)行各種任務集;綠色推進公司專注于研發(fā)電推進系統(tǒng),其專有的增材制造方法可支持快速修改產(chǎn)品以適應不同的飛機、任務和要求。通過將兩家公司的技術(shù)集成到模塊化無人機系統(tǒng)中,有望實現(xiàn)增材制造無人機機身和發(fā)動機的100%快速低成本大規(guī)模增材生產(chǎn),并支持多種有效載荷,確保能夠在最具挑戰(zhàn)性的環(huán)境中執(zhí)行任務。
【述析】聚焦實戰(zhàn)化能力,各國正在加速無人集群作戰(zhàn)系統(tǒng)全面融入作戰(zhàn)體系,對低成本高效批產(chǎn)的需求劇增。該項合作體現(xiàn)了低成本大規(guī)模生產(chǎn)無人機的關鍵要素,即模塊化、智能化、增材制造。增材制造無模具整體化成形的優(yōu)勢能夠確保滿足無人系統(tǒng)的輕量化要求,并為高效制造功能結(jié)構(gòu)提供可能。此外,天生具有數(shù)字化屬性的增材制造技術(shù),能夠在批量生產(chǎn)過程中與自動化、網(wǎng)絡化技術(shù)結(jié)合形成分布式生產(chǎn)能力,進一步提升對生產(chǎn)過程的高效洞察與柔性管控,是實現(xiàn)低成本、可消耗無人系統(tǒng)快速生產(chǎn)的優(yōu)質(zhì)選擇。
洛·馬公司投資先進機器人鈑金成形技術(shù)
1月,洛?馬公司風投部門向美國Machina實驗室公司投資,支持其開發(fā)無模機器人板材成形工藝,替代依賴定制模具的傳統(tǒng)鈑金成形方法,以大幅縮短交付周期并降低制造成本。該方案使用雙機械臂成形金屬板材,無需設計制造模具,靈活性強,可將零件生產(chǎn)周期從50周縮短到數(shù)小時,節(jié)省成本達百萬美元。制造平臺通過軟件驅(qū)動,結(jié)合了機器人和人工智能技術(shù),可將CAD文件轉(zhuǎn)換為機器人運行路徑,并利用大量人工智能驅(qū)動的傳感器收集數(shù)據(jù),逐步使板材成形為最終零件。系統(tǒng)在零件成形過程中會創(chuàng)建包含所有制造過程信息的數(shù)字孿生,以確保工藝特性和零件鑒定信息的準確性。
【述析】
除復材成形、增材制造和裝配等應用外,先進信息技術(shù)和自動化技術(shù)也在為勞動密集型的傳統(tǒng)制造技術(shù)帶來轉(zhuǎn)型升級契機。初創(chuàng)公司Machina實驗室正在探索使用人工智能和機器人技術(shù)從根本上改變金屬板材成型行業(yè),其雙7軸機器人協(xié)作的鈑金成形解決方案簡化了切割和彎曲金屬板的過程,人工智能則能夠進一步賦能路徑優(yōu)化、缺陷識別和系統(tǒng)預測性維護等,優(yōu)于依賴定制模具或沖模的傳統(tǒng)成型方法。洛·馬公司對該技術(shù)的青睞,凸顯了航空裝備制造商對高精度、短周期、柔性制造技術(shù)的密切關注,也是其在先進制造領域?qū)嵤?shù)字化轉(zhuǎn)型戰(zhàn)略的重要投資。
洛?馬公司開發(fā)用于機身制造的自主認知機器人
6月,洛?馬公司將其工業(yè)機器人與Xaba公司專有的物理信息深度人工神經(jīng)網(wǎng)絡模型xCognition集成,測試了xCognition的“合成大腦”如何賦予機器人更強大的智能功能,以及對其機體和即將執(zhí)行的任務的理解,同時確保達到所需的質(zhì)量和公差。測試包括兩個階段,一是評估機器人在使用和不使用xCognition系統(tǒng)時保持準確和一致的軌跡定位的性能;二是在具有指定位置公差的鋁制試驗板上進行一組鉆孔試驗。結(jié)果表明,xCognition將機器人的準確性和一致性提高了10倍,使得工業(yè)機器人能夠高效執(zhí)行當前必須更昂貴、不靈活的數(shù)控機床完成的關鍵制造操作。
【述析】
ChatGPT、Sora等工具的橫空出世切實展現(xiàn)了人工智能的巨大能量,工業(yè)制造中的人工智能應用也在不斷擴展,典型代表之一的初創(chuàng)公司Xaba正專注于使用工業(yè)人工智能將任意工業(yè)機器人變身“生成式機器人”,使其在生成程序和執(zhí)行焊接、鉆孔、組裝和增材制造等任務時變得更加智能和自主。這一解決方案顛覆了當前的自動化制造業(yè)務模式,使傳統(tǒng)工業(yè)機器人和協(xié)作機器人能夠?qū)崿F(xiàn)成本更高的高精度機床的性能??梢韵胂笙?,未來的航空制造是否會是:操作員口述一個簡單的需求指令,然后機器人總動員——自主生成零部件并完成整架飛機的完美建造?
英國先進制造中心開發(fā)機器人布線與缺陷檢測解決方案
5月,英國謝菲爾德大學先進制造研究中心與Q5D技術(shù)機器人公司合作,開發(fā)了可計算工件的位置和旋轉(zhuǎn)角度以及實時嵌入式布線缺陷檢測解決方案,支持5軸機器人自動完成復雜飛機部件布線和質(zhì)量檢測。該解決方案利用基于立體視覺技術(shù)的深度相機和Halcon計算機視覺開發(fā)工具,構(gòu)建點云表面模型,準確計算工件位置和旋轉(zhuǎn)角度,并將缺陷檢測算法與二維高分辨率灰度圖像結(jié)合,檢測電線斷裂、電線壓碎、電線絕緣層剝落等質(zhì)量問題。經(jīng)驗證,實現(xiàn)了工件位置計算精度在0.5毫米,旋轉(zhuǎn)角度誤差小于0.6度,不同角度工件的裸線缺陷檢出率達到100%。
【述析】
飛機中的復雜管路和長達數(shù)百公里的電線安裝,是智能視覺系統(tǒng)發(fā)揮作用的主戰(zhàn)場。該研究成果是Q5D公司牽頭的名為LiveWire的研發(fā)項目的一部分,該項目受“創(chuàng)新英國”機構(gòu)資助,旨在實現(xiàn)航空工業(yè)線束生產(chǎn)和檢測的自動化。經(jīng)驗證,機器人平臺與視覺系統(tǒng)的集成為布線檢測帶來了更高的可靠性和靈活性,未來,這一技術(shù)概念有望嵌入任意機器人作業(yè)系統(tǒng),將人從大量繁瑣低效的肉眼檢測和離線檢測工作中解放出來,助力工廠形成數(shù)字化、自動化的質(zhì)量管控能力。
美軍使用移動式、自主冷噴涂系統(tǒng)進行H-1直升機維修
3月,美海軍陸戰(zhàn)隊使用新型移動式、自主冷噴涂系統(tǒng)對H-1直升機的組合齒輪箱和滑管進行維修,以縮短飛機維修時間,降低成本。與傳統(tǒng)維修方式相比,該系統(tǒng)的優(yōu)勢包括消除待維修零部件尺寸限制,提升飛機現(xiàn)場維修能力;無需拆卸和搬運零部件,可維修磨損零部件并重新使用,節(jié)省維修時間和成本;可以通過編程自動運行或者由專業(yè)技術(shù)人員手動操作,操作更加靈活。該系統(tǒng)在各飛機平臺均具有應用潛力,有望推廣至整個海軍航空維修部門。
【述析】
快速維修保障是保持、恢復和提高作戰(zhàn)部隊戰(zhàn)斗力的重要因素。面對依賴海外供應鏈導致的鍛件交貨期長等問題,美軍換道將增材制造作為強化供應鏈韌性、快速搶修作戰(zhàn)裝備的重要抓手。冷噴涂技術(shù)通過將粉末以超聲速沖擊受損零件表面,能夠在基體表面形成牢固附著的致密材料從而恢復零件尺寸。美陸海空三軍均已利用冷噴涂技術(shù)開展高價值航空部件修復,并持續(xù)研究提升冷噴涂平臺的可移動性、自主性,以期為維修基地和作戰(zhàn)部隊提供更快速、靈活便捷且低成本的再制造能力,提升作戰(zhàn)裝備經(jīng)濟性和戰(zhàn)備完好性。
中國航空工業(yè)發(fā)展研究中心
陰鵬艷、劉亞威、周航、戴晟、杜麗婷