銅渣處理與資源化技術
(1)銅渣的火法貧化
返回重熔和還原造锍是銅渣火法貧化的主要方式。爐渣返回重熔可回收銅得到的銅锍返主流程,爐渣的鈷、鎳回收采取在主流程之外的單獨還原造鏡。渣貧化方法很多,熔煉工藝是確定爐渣貧化工藝技術的主要因素,含銅爐渣的火法貧化基于以下反應:
3FeO+FeS——10Fe0+SO (6-6)
(Fe,Co,Ni)0FeO+C—→CoO+NiO+3FeO+CO (6-7)
2(Co,Ni)0SiO+2FeS——2FeOSiO+2(Co,Ni)S (6-8)
為降低渣中FeO含量,還原可使FeO轉(zhuǎn)化為FeO并與加入的石英熔劑造渣以改善銅锍的沉降分離,并產(chǎn)生了一些新的貧化方式。①反射爐貧化:反射爐是爐渣貧化傳統(tǒng)方法,在爐頂采用氧/燃燒噴嘴的反射筒形反應器,將含銅和磁性氧化鐵礦物分批裝人,通過風口噴粉煤、油或天然氣進入熔池,還原磁性氧化鐵使含量降低到10%,然后分離出熔融渣中銅锍,這種方法至今仍在日本小名浜冶煉廠和智利的卡列托勒斯煉銅廠應用。②電爐法貧化:用電爐提高熔體溫度使渣中銅的含量降低,同時還原熔融渣中氧化銅,回收熔渣中細顆粒銅。電爐貧化不僅可處理各種成分的爐渣,而且還可以處理各種返料,電能在電極間的流動產(chǎn)生攪拌作用,可促使渣中的銅粒凝聚長大。③真空貧化:爐渣真空貧化使諾蘭達富氧熔池爐渣1/2~2/3的渣層含銅量從5%降到0.5%以下,真空貧化可迅速消除或減少Fe。O而降低渣的熔點、黏度和密度,以提高渣-锍間的界面張力而促進渣-锍分離。真空的作用是迅速脫除渣中的SO氣泡,利用氣泡的迅速長大上浮對熔渣進行強烈攪拌,增大了锍滴碰撞合并,但存在的主要問題是成本較高和操作復雜。④渣桶法:用渣桶作為沉淀池為常用的降低廢渣含銅的一種最簡便的方法,其關鍵是保持桶內(nèi)爐渣溫度,回收桶底富集的部分渣或渣皮再處理,利用渣的潛熱來實現(xiàn)銅滴沉降和晶體粗化。⑤熔鹽提?。豪勉~在渣中與銅锍中的分配系數(shù)差異,以液態(tài)銅锍為提取相使其與含銅爐渣充分接觸,從而提取溶解和夾雜在渣中的銅,該方法用于處理哈薩克斯坦的瓦紐科夫法產(chǎn)生的爐渣取得較好的效果,此外最近熔鹽提取出現(xiàn)了直流電極還原和電泳富集等方法。
(2)爐渣選礦
利用金屬賦存相表面親水、親油性質(zhì)及磁學性質(zhì)的差別,通過磁選和浮選分離富集。銅渣黏度大,阻礙銅相晶粒的遷移聚集使晶粒細小,造成銅相中硫化銅的含量下降,使銅選礦困難。①浮選法:從富氧閃速熔煉渣和轉(zhuǎn)爐渣中浮選回收銅在工業(yè)上已廣泛應用,浮選法銅收率高且能耗低,將FeSO▲等雜質(zhì)除去可降低吹煉過程石英消耗,回收率達90%以上,尾渣含銅0.3%~0.5%。②磁選法:銅渣中強磁相為鐵合金和磁鐵礦,鈷、鎳在鐵磁礦物中集中,銅存在于非磁相,世界上多家銅冶煉廠用選礦方法回收轉(zhuǎn)爐渣中的銅。
(3)濕法浸出
濕法過程可克服火法貧化過程的高能耗以及產(chǎn)生廢氣污染的缺點,其分離的良好選擇性更適合于處理低品位銅渣。①直接浸出:煉銅爐渣中Cu、Ni、Co、Zn 等金屬的礦物可經(jīng)氧氣氧化而溶于稀硫酸介質(zhì)中。隨著鐵的溶解,損失在渣中的銅及占據(jù)部分Fe晶格的鈷、鎳等被釋放出來,實踐中采用0.7mol/L硫酸在氧壓0.59 MPa及130℃條件下單段浸出轉(zhuǎn)爐渣,銅浸出率達92%,鎳鈷浸出率大于95%。②間接浸出:預處理可改性銅渣中的有價金屬賦存狀態(tài),使其易于分離回收,氯化焙燒和硫酸化焙燒為常用的方法,焙燒產(chǎn)物直接水浸,酸性FeCl浸出經(jīng)還原焙燒的閃速爐渣及轉(zhuǎn)爐渣的鎳鈷浸出率分別達95%和80%。③細菌浸出:細菌浸出能浸溶硫化銅,因其具有一系列優(yōu)點而快速發(fā)展。但細菌浸出的最大缺點是反應速度慢、浸出周期長,通過加入某些金屬(如Co、Ag)催化加速細菌氧化反應的速率,使金屬陽離子取代礦物表面硫化礦晶格中原有的Cu2t、Fe3+等離子以增加硫化礦的導電性,從而加快了硫化礦的電化學氧化反應速率。
(4)用于水泥和建筑行業(yè)
煉銅爐渣水淬后是一種黑色、致密、堅硬、耐磨的玻璃相。密度為3.3~4.5g/cm3,孔隙率50%左右,細度3.37~4.52,屬粗砂型渣。表6-19為銅渣在水泥工業(yè)及建筑行業(yè)的應用情況。
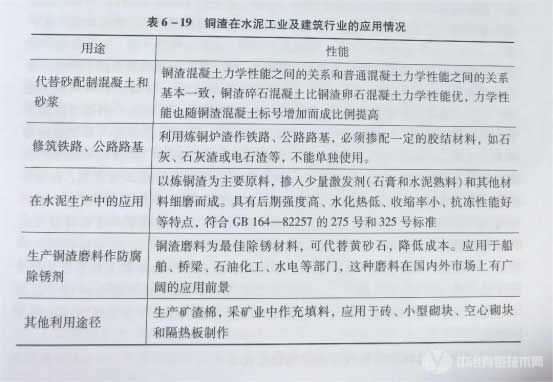
爐渣的選擇性析出是利用爐渣的高溫熱能,通過合理控制溫度、添加劑、液體的運動行為改變渣的組成和結(jié)構(gòu),從而實現(xiàn)渣中有價組分的回收和資源化,已成功應用于含鈦高爐渣、硼鐵礦等復雜礦物的處理。向含銅熔渣加入還原劑首先降低渣的黏度促進銅的沉降,待銅沉降到一定程度后使渣迅速氧化,提高磁性氧化鐵的含量,緩冷粗化晶粒,磁選分離含鐵組分,實現(xiàn)銅渣中殘余銅的含量從5%降低到0.5%以下,渣中Fe,O4含量從26.8%提高到50%以上。
(6)銅冶煉高砷物料中砷的脫除與固化——穩(wěn)定化技術
砷是伴生于銅精礦中且對銅冶煉過程及環(huán)境保護極其有害的元素。我國銅精礦行業(yè)標準(YS/T318—2007)將銅精礦分為5級,1級至5級銅精礦As含量分別限定為不大于0.1%、0.2%、0.2%、0.3%、0.4%。國家強制性標準《重金屬精礦產(chǎn)品有害元素限額規(guī)范》規(guī)定,銅精礦中As含量不得大于0.5%。
近年來,由于優(yōu)質(zhì)銅資源減少,國內(nèi)生產(chǎn)及國外進口銅精礦中砷含量均呈現(xiàn)上升趨勢,根據(jù)有關銅冶煉廠報道數(shù)據(jù)估計,目前我國銅冶煉廠所用銅精礦,平均砷含量為0.25%。2013年,我國精煉銅產(chǎn)量達到663萬t,其中礦產(chǎn)精煉銅產(chǎn)量約400萬t。據(jù)此推算,我國隨銅精礦進入銅冶煉系統(tǒng)的砷量達4.0萬t/a。
砷在銅精礦中主要以硫化物形式存在,如硫砷銅礦、砷黝銅礦、黝銅礦、黝銅礦、含砷黃鐵礦、砷黃鐵礦、雄黃和雌黃等。在銅火法冶煉中,砷分散分布于煙塵、爐渣、銅锍或粗銅中,其行為與原料成分、冶煉工藝及技術條件等相關,十分復雜,但其最終出口主要有以下幾處(以奧圖泰閃速富氧熔煉為例):熔煉爐渣(電爐渣),占進入系統(tǒng)總砷量的30%,如果直接外銷,這部分砷將開路,如果對電爐渣進一步選礦處理,這部分砷將大部分(約80%)隨渣精礦返回熔煉系統(tǒng);吹煉白煙塵,占進入系統(tǒng)總砷量的10%,在火法煉銅各類煙塵中,白煙塵含砷最高,達15%左右,且含有其他有價金屬,因此大部分企業(yè)都將其單獨或外銷處理以便從系統(tǒng)中開路部分砷;熔煉和吹煉SO煙氣凈化污酸,所含砷量占進入系統(tǒng)總砷量的40%左右,一般企業(yè)將其硫化沉淀,得到硫化砷渣,再進一步濕法處理生產(chǎn)白砷產(chǎn)品或返回配料或外銷;粗銅,所含砷占進入系統(tǒng)砷總量的20%左右,在電解精煉溶液凈化中,砷大部分進入黑銅板或黑銅粉返回系統(tǒng)。隨著銅精礦砷含量的升高,產(chǎn)生了兩方面的問題:第一是系統(tǒng)中砷開路不足,形成累積導致硫酸及電解銅生產(chǎn)受到不利影響。一般是將含砷較高的物料,如白煙塵、黑銅粉和硫化砷渣等,從系統(tǒng)中開路出來,單獨處理。國內(nèi)外都有成熟的技術和工業(yè)實踐,如美國肯尼科特公司Garfield煉銅廠、智利國家銅公司(Codelco)下屬含砷煙塵處理廠、我國云南銅業(yè)公司等。第二是砷的安全環(huán)保處置問題,目前在我國還未能很好解決。
(7)銅冶煉高砷物料中砷的脫除與穩(wěn)定化
在火法煉銅中,砷從廢氣、廢水途徑的排放,通過采用嚴格的環(huán)??刂拼胧?,均能實現(xiàn)達標,目前至少技術上已無問題。存在的問題是隨著優(yōu)質(zhì)銅資源的減少,復雜、低品位銅礦的開發(fā),隨銅精礦帶入冶煉廠的砷量日益增大,而安全穩(wěn)定的砷開路出口僅有電爐貧化后水淬熔煉渣,或熔煉及吹煉渣選礦尾礦,對多數(shù)煉銅廠而言,會造成砷開路不足而在系統(tǒng)中累積,影響生產(chǎn)、環(huán)保和衛(wèi)生。前已述及,在銅資源日趨緊張的情況下,爐渣選礦已成為從銅冶煉渣中回收銅的主流技術,在我國得到普遍應用。在爐渣選礦的情況下,爐渣中的砷約80%進入渣精礦返回熔煉,選礦尾礦中僅能開路進入系統(tǒng)總砷量的約6%(30%×20%),這將使砷在系統(tǒng)內(nèi)循環(huán)累積的問題更為凸顯。因此,從硫化砷渣、高砷煙塵或黑銅粉等火法煉銅高砷物料中將砷脫除開路,然后將銅等有價金屬回收返回系統(tǒng),已成為發(fā)展趨勢,目前在國內(nèi)外很多原料含砷較高的煉銅廠,正是通過這一技術措施解決了砷累積的問題。仍存在的問題在于,砷屬劇毒、致癌和“過?!痹?,冶煉回收的砷遠遠超過其應用所需,因此大部分的砷只能固化后堆存,而這一問題目前在我國仍未很好解決。
據(jù)美國地質(zhì)調(diào)查局(USGS)報道,2011年全球主要砷生產(chǎn)國白砷(砒霜,As,O)產(chǎn)量為5.2萬t,其中,我國是最大生產(chǎn)國,達2.5萬t。據(jù)估算,我國隨有色金屬精礦或礦石進入冶煉系統(tǒng)的砷量,每年至少達到10萬t以上,而隨爐渣帶走的量,估計只有約3萬t,其余除少量隨含砷廢水凈化渣帶走外,大部分富集于各類高砷物料中,或在系統(tǒng)中循環(huán)累積,或轉(zhuǎn)化成白砷產(chǎn)品,甚至還有部分流向中小企業(yè),造成嚴重的安全與環(huán)境隱患,這也正是近年來我國砷污染事故頻發(fā)的原因之一。
從銅冶煉高砷物料中脫除的砷,全部轉(zhuǎn)化成白砷或金屬砷產(chǎn)品,是沒有銷路和經(jīng)濟效益的,使其固化—穩(wěn)定化后堆存是主要的方向。針對這一問題,國內(nèi)外開展了大量研究,國外研究主要集中在加拿大、日本和智利等國的學術與產(chǎn)業(yè)界。國內(nèi)近年來也有一些研究和實踐。曾研究過使含砷物料與高溫熔融爐渣混合,將砷固化在爐渣玻璃體中而實現(xiàn)穩(wěn)定化,結(jié)果表明,在這高溫過程中,砷化合物會大量揮發(fā),由此也證明玻璃包封方案不可行。水泥包封固化是一種可行的方案,但其固砷產(chǎn)物量太大,成本過高,并未得到廣泛采用。硫化砷、砷酸鈣在堆存中與空氣和水接觸,均會發(fā)生分解而不能穩(wěn)定固化砷。這種方法沉砷渣含砷低、含水高,只適用于含砷濃度相對較低的廢水處理,而不適合于作為高砷物料中脫除砷的固化方案。
在水熱或常溫條件下,通過對結(jié)晶過飽和度的控制,均可使溶液中的As(V)和Fe(Ⅲ)以臭蔥石沉淀。目前,智利國家銅公司已建成一家處理高砷銅煙塵的工廠,采用加拿大McGill大學Demopolos教授研發(fā)的分步控制過飽和度的方法,使砷從含F(xiàn)e(Ⅲ)的浸出液中以臭蔥石沉淀堆存,然后再從沉砷后液中采用萃取法回收銅、鋅等有價金屬,目前年處理高砷煙塵5~7萬t。最近的研究也表明不同條件下沉淀的臭蔥石,其穩(wěn)定性相差甚大,這是值得進一步深入研究的問題。
我國是世界上最大的礦銅冶煉生產(chǎn)國。目前,僅有部分砷轉(zhuǎn)化為白砷產(chǎn)品。對銅冶煉高砷物料中砷的脫除與固化—穩(wěn)定化,雖然有一些研究,但在工業(yè)應用上還未起步,應引起重視并盡快付諸行動,為砷的減排和污染防治奠定堅實基礎。